Interview
Elektronik unter Stress: Wie die Verschärfung von Umweltbedingungen Frühausfällen von elektronischen Systemen vorbeugen kann
»Kalte Winter mit starkem Frost, heiße Sommertage mit mehr als 40 °C oder hohe Niederschlagsmengen – extreme Temperaturen und Feuchte können dramatische Auswirkungen auf elektronische Komponenten und Module haben, die zu Defekten und zum vorzeitigen Ausfall ganzer Systeme führen können«, erklärt Kerstin Kreyßig vom Fraunhofer ENAS. Als Expertin für Zuverlässigkeitstests weiß sie, Wärme und Kälte optimal einzusetzen, um elektronische und mikroelektronische Baugruppen auf Herz und Nieren zu prüfen und Mängel frühzeitig zu erkennen. Im Interview erklärt die Ingenieurin, welchen Mehrwert thermische und klimatische Belastungstests für Kunden aus Industrie und Forschung bieten und welche Rolle dabei ein unterirdisches Labor spielt.
Seit vielen Jahren untersuchen und prüfen Sie am Fraunhofer ENAS den Einfluss rauer Umweltbedingungen auf Elektroniksysteme. Welche Motivation steckt hinter diesen Arbeiten?
In unserem Alltag begegnen uns elektronische Komponenten und Bauteile auf Schritt und Tritt, auch wenn sie uns häufig auf den ersten Blick nicht bewusst sind. Hochsensible Technologien stecken in vielen Konsumgütern ebenso wie in industriellen Anlagen und Automobil-Anwendungen. Überall steigt der Einsatz von Elektronik, um Produkte beispielsweise mit neuen Funktionalitäten auszustatten. Elektronische Baugruppen und Systeme sollen dabei stets einwandfrei funktionieren und mindestens so langlebig wie das Produkt selbst sein. Um die Gefahr zu früher Ausfälle bereits in der Entwicklung zu identifizieren und ihre Ursache zu beseitigen, setzen wir die Prototypen unter Stress. Mithilfe von Zuverlässigkeitstests simulieren wir dabei raue Umweltsituationen experimentell, denen die Produkte im Betrieb ausgesetzt sein können. Dazu konfrontieren wir sie in unseren Tests mit extremen Temperaturen, Feuchte oder Vibrationen, um damit typische Alterungs- und Schädigungsprozesse, die im Betrieb und bei normaler Nutzung unvermeidlich auftreten, zeitbeschleunigt zu provozieren.
Warum ist das sinnvoll?
Die Produkte sollen unter realen Einsatzbedingungen eine Lebensdauer von beispielsweise zehn Jahren haben und erst nach dieser Nutzungsdauer durch Verschleiß oder Materialermüdung der elektronischen Bauteile altersbedingt ausfallen. Im Rahmen der Technologie- und Produktentwicklung sind diese Zeiträume jedoch sehr lang. Deshalb reduzieren wir sie durch unsere Tests auf wenige Monate. Dabei achten wir darauf, dass die Alterungsprozesse zwar beschleunigt ablaufen, aber nicht zu anderen Ausfällen führen, als typischerweise bei normaler Nutzung.
Welche Erkenntnisse liefern solche Zuverlässigkeitstests, bei denen verschiedene Temperaturen oder Feuchte eingesetzt werden?
In Elektronikbaugruppen müssen sehr viele unterschiedliche Werkstoffe optimal zusammenwirken. Halbleiter, Glas und Keramik werden mit den verschiedenen Metallen wie Kupfer, Aluminium und Lot sowie organischen Materialien wie Klebstoff, Vergussmasse und Glasfaser-verstärktem Epoxidharz auf engstem Raum zusammengefügt. Nur, wenn alles optimal aufeinander abgestimmt ist, kann das elektronische System über eine lange Zeit fehlerfrei funktionieren.
Allerdings sind Temperaturzyklen im Betrieb von Elektronikaufbauten unvermeidlich. Sie werden durch Umweltbedingungen, aber auch durch die Eigenerwärmung der Systeme selbst verursacht. Durch Temperaturwechsel können in den Baugruppen aufgrund der vielen verschiedenen Materialien thermisch-mechanische Spannungen entstehen. Diese können so groß werden, dass sich Risse bilden, die sich ausbreiten und schließlich zu Defekten führen. Das können beispielsweise Brüche der Lotkontakte, Ablösungen von Bonddrähten, Risse zwischen der Vergussmasse des Gehäuses und dem Halbleiterchip oder der metallischen Bodenplatte sein. Feuchte senkt darüber hinaus die Klebekraft der Vergussmasse und erhöht die Rissgefahr zusätzlich. Diese Defekte können nicht nur den Ausfall des betroffenen Bauelements, sondern des gesamten Systems bewirken. Genau hier setzen unsere Tests an. Sie helfen dabei, frühzeitig solche Ausfallpotentiale aufzudecken.
Welcher Mehrwert ergibt sich dadurch für Forschende und Hersteller von Elektroniksystemen?
Belastungstests mit unterschiedlichen Temperaturen und klimatischen Bedingungen sind wichtige Säulen in der Zuverlässigkeitsbewertung und Lebensdauervorhersage von Produkten und daher unverzichtbar in der Produktentwicklung. Das Wissen um Schwachstellen können Hersteller in die Konstruktion, die Werkstoffauswahl und ihre Herstellungsprozesse einfließen lassen noch bevor ein Produkt in die Serienproduktion überführt wird. Damit wird sichergestellt, dass nur Produkte mit optimierten Eigenschaften und Lebensdauern auf den Markt gebracht werden. Das spart nicht nur wertvolle Zeit und Ressourcen, sondern auch teure Rückrufaktionen und senkt die Zahl nötiger Gewährleistungen, was auch die Kundenzufriedenheit und letztlich die Reputation des Herstellers stärkt.
Wie werden elektronische Komponenten und Module am Fraunhofer ENAS im Detail getestet?
Es kommen verschiedene Mess- und Prüfsysteme zum Einsatz, um die Auswirkungen von schnellen Temperaturschocks, langsameren Temperaturwechseln und dauerhaften Klimabelastungen auf elektronische Aufbauten zu simulieren und zu testen. Temperaturen, Prüfdauern und die Anzahl an Zyklen, denen die Prüflinge ausgesetzt werden, stimmen wir dabei individuell auf das künftige Anwendungsszenario des elektronischen Bauteils ab. Außerdem wählen wir jeweils die optimalen Bedingungen aus einem Industriestandard aus, damit die erzielten Ergebnisse mit den bereits vorhandenen Resultaten vergleichbar sind.
Mit unserem Zwei-Kammer-Schockofen können wir Proben zum Beispiel sehr raschen Temperaturwechseln zwischen -40 °C und 125 °C aussetzen. Dieser Test spielt für Automobil-Anwendungen eine wichtige Rolle. Er simuliert den Kaltstart in Nord-Finnland, der für Elektronikaufbauten aufgrund der extremen Temperaturen eine besonders große Herausforderung darstellt. Die Verweildauer in der Kalt- und Warmkammer unseres Schockofens richtet sich nach dem Volumen der Baugruppe. Die Anzahl der Testzyklen, die die Elektronik absolvieren muss, hängt von den konkreten Ausfallmodi ab, die mit der betreffenden Prüfung untersucht werden sollen. Durch das kontinuierliche Messen der elektrischen Widerstände direkt an den Bauteilkontakten können wir den jeweiligen Ausfallzeitpunkt genau ermitteln. Er zeigt sich in Widerstandserhöhungen zumeist unmittelbar nach dem Wechsel der Kammern, tritt oft aber nur kurzzeitig auf. Die beiden Seiten eines gerissenen Kontakts, zum Beispiel, können sich danach auch wieder schließen und die elektrische Verbindung wieder herstellen. Mit solchen Kontaktunterbrechungen ist die Funktion der Elektronik jedoch nicht mehr zuverlässig gegeben. Unsere kontinuierliche in-situ Messung kann auch solche kurzzeitigen Unterbrechungen sicher erkennen. Am Ende der Tests entsteht eine Statistik zum Ausfallverhalten der Bauteile. Aus der Verteilung der Ausfallzeitpunkte der einzelnen Prüflinge kann von der Stichprobe auf die charakteristische Lebensdauer der gesamten Produktreihe geschlossen werden.
Außerdem verfügen wir über ein kombiniertes Klima-Temperatur-Schwingungs-System, mit dem wir Proben beim elektrischen Stressen und Überwachen gleichzeitig Feuchtigkeit zwischen 10% und 95%, Temperaturwechseln und Vibrationen aussetzen können. Das simuliert eine breite Palette verschiedenster Belastungen, wie sie Bauelemente in ihren verschiedenen Einsatzszenarien erleben, in denen sie im Sommer wie im Winter sowie bei Nebel, Regen oder Eis einwandfrei funktionieren müssen. Für Hersteller von Automobilelektronik, Maschinensteuerungen in der Metall- und Chemieindustrie und für Smart-Grid Anwendungen sind diese kombinierten Tests besonders interessant. Gemeinsam mit Herstellern aus diesen Branchen arbeiten wir an neuen Teststandards, damit die Ergebnisse industrieweit vergleich- und bewertbar sind.
Wenn wir noch deutlich höhere Temperaturen erreichen wollen, dann nutzen wir unser Hochtemperatur-Ofensystem, das Temperaturwechsel von -80 °C bis 500 °C ermöglicht. Solche hohen und schnellen Temperaturwechsel sind nicht nur für spezielle Industrieanwendungen und die Raumfahrt relevant. Neue Leistungsbauelemente für Inverter in E-Fahrzeugen bestehen aus Siliziumkarbid oder Galliumnitrid anstatt aus dem bisher verwendeten Silizium. Sie können im regulären Betrieb Temperaturen von bis zu 300 °C dauerhaft standhalten. Eine Beschleunigung der Alterung erfordert das Prüfen bei noch höheren Temperaturen.
Insgesamt können wir in unserem Prüflabor alle klimatischen Umwelteinflüsse simulieren, denen Elektronik in äußerst herausfordernden Anwendungen ausgesetzt werden sollen – egal ob bei Schnee und Eis in Alaska oder in der Hitze der Sahara. Dabei können wir die Belastungen Temperatur, Feuchte und Vibration sehr realistisch gleichzeitig wirken lassen, um gezielt herauszufinden, ob elektronische Systeme bei diesen rauen Bedingungen so lange wie vorgesehen fehlerfrei funktionieren.
Zuverlässigkeitsuntersuchungen führt das Fraunhofer ENAS aber nicht nur in Laborumgebungen durch, sondern auch an einem ungewöhnlichen Ort, nämlich tief verborgen unter der Erde. Was genau hat es damit auf sich?
Für unsere Kunden führen wir auch Langzeittests von elektronischen Bauteilen durch. Dafür haben wir in einem ehemaligen Bergwerk das europäische Labor für Langzeitzuverlässigkeitsuntersuchungen eingerichtet. Darin können wir Zuverlässigkeitstests durch die Nutzung der natürlichen Umgebungsbedingungen des Bergwerks mit energetisch höchsteffizienten Temperaturwechseln zwischen 12 °C und 100 °C durchführen. Die Proben werden dabei zunächst in einem Ofen in ca. einer Stunde auf 100 °C aufgeheizt. Anschließend werden sie durch die Umgebungstemperatur des Bergwerks in ca. sechs Stunden abgekühlt. Nach sieben Stunden beginnt der nächste Zyklus. Das entspricht der typischen Benutzung eines Fahrzeugs, bei der nach einer kurzen Fahrtzeit ein längeres Parken und damit ein über mehrere Stunden dauernder »Stillstand« folgt. Im Anschluss wird das Fahrzeug erneut bewegt und die Fahrt fortgesetzt. Diese feldnahen Realtests haben wir inzwischen für die Gesamtlebensdauer von 15 Jahren praktisch durchgeführt, wie sie für Elektronik der Anwendungsfelder Automobil, Industrie und Energie typisch sind. Solche ultra-langfristigen Versuche helfen uns, die Richtigkeit unserer beschleunigenden Labortests zu verifizieren und diese noch weiter zu verbessern, damit sie die Phänomene der Kriechermüdung in den verschiedenen Lot- und Sinterverbindungen der Elektronik, zum Beispiel mit Rissen, Brüchen und Delaminationen, korrekt nachbilden.
Herzlichen Dank, Frau Kreyßig, für dieses Gespräch und die Einblicke in die Lebensdauerprognose von elektronischen Systemen.
Wollen Sie mehr über unsere Testdienstleistungen erfahren? Dann nehmen Sie noch heute Kontakt mit uns auf.
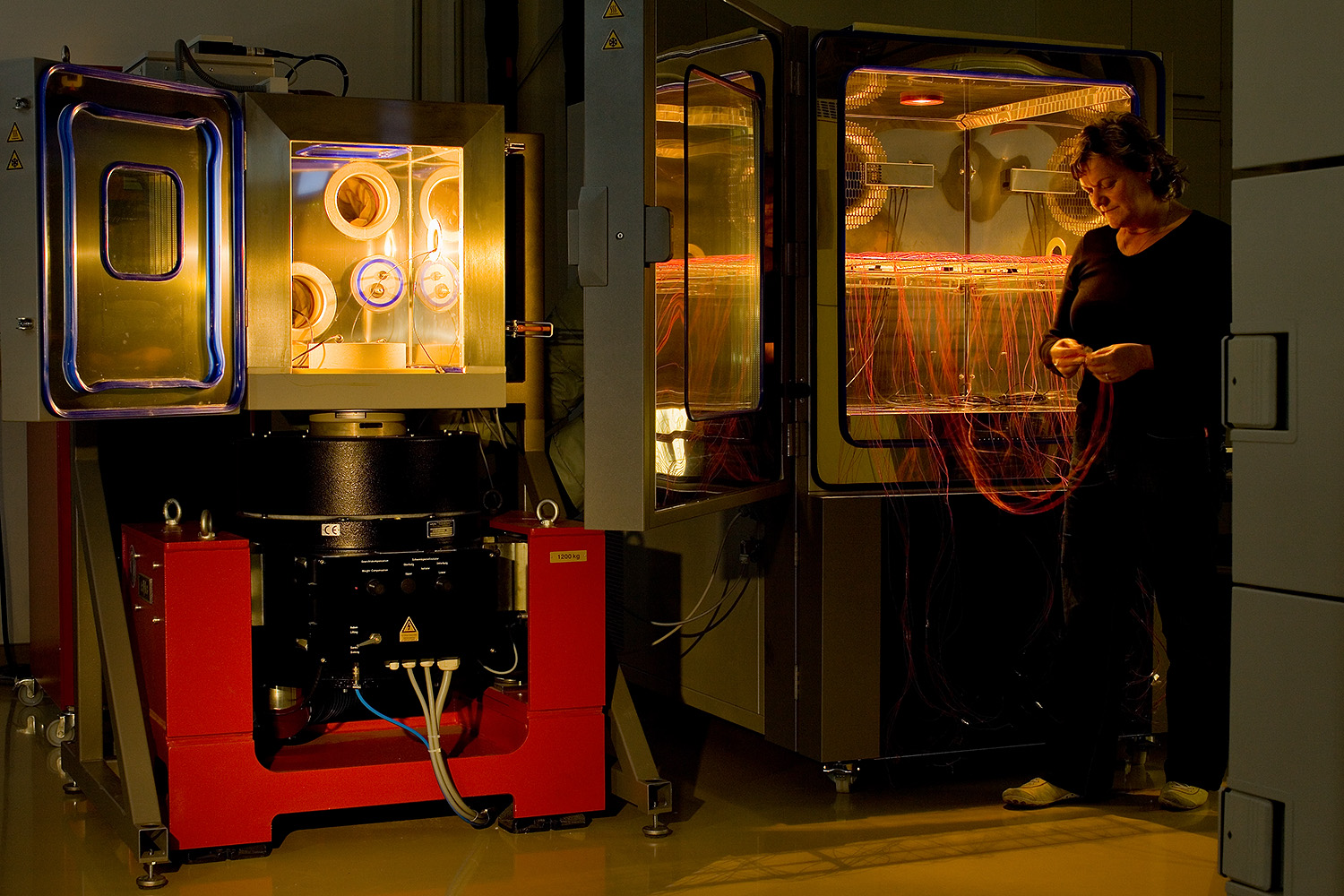
Letzte Änderung: