Interview
Electronics under stress: How extreme environmental conditions can prevent early failure of electronic systems
“Cold winters with heavy frosts, hot summer days reaching 40 °C or more or heavy rainfall – extreme temperatures and moisture can have dramatic consequences for electronic components and modules, leading to defects and the early failure of entire systems,” explains Kerstin Kreyßig from Fraunhofer ENAS. As an expert in reliability tests, she knows how to use heat and cold effectively in order to put electronic and microelectronic assemblies through their paces and detect defects at an early stage. In this interview, the engineer explains how thermal and climatic stress tests provide added value for customers from industry and research and how an underground laboratory plays its part.
You have been studying and testing the influence of harsh environmental conditions on electronic systems for many years at Fraunhofer ENAS. What is the motivation behind this work?
We encounter electronic components and parts at every turn in our day-to-day lives, though we are often unaware of them at first glance. Highly sensitive technologies can be found in many consumer products as well as in industrial systems and automotive applications. The use of electronics is increasing everywhere, as they enable products to be equipped with new functions, for example. Electronic assemblies and systems need to work perfectly at all times and last at least as long as the product itself. To enable the risk of early failure to be identified during the development phase and its cause to be rectified, we put the prototypes under stress. In our reliability tests, we carry out experiments to simulate harsh environmental situations that the products may be exposed to during operation. We subject the products to extreme temperatures, moisture or vibrations in order to provoke typical aging and damage processes – that will inevitably occur during operation and in normal use – in an accelerated manner.
Why is this useful?
The products are expected to have a service life of ten years, for example, under real-life operating conditions. It is only after this life span that we would expect wear and tear or material fatigue on the electronic components to lead to age-related failure. In the context of technology and product development, however, these timescales are very long, which is why we reduce them down to a few months in our tests. We make sure that, even though the aging processes are accelerated, they only result in the failures that would typically occur during normal use.
What kind of insights do you get from exposing products to different temperatures or moisture in these reliability tests?
Electronic assemblies comprise many different materials which all need to work together perfectly. Semiconductors, glass and ceramics are combined with various metals such as copper, aluminum and solder as well as organic materials such as adhesive, sealing compound and glass-fiber reinforced epoxy resin in the smallest of spaces. Everything has to be perfectly coordinated in order for the electronic system to keep functioning correctly over a long period.
However, temperature cycles are inevitable during the operation of electronic assemblies, caused by both environmental conditions and the self-heating of the systems themselves. Due to the use of many different materials in the assemblies, temperature changes can result in thermal-mechanical stresses. If these stresses are great enough, they can cause cracks to form which then expand and ultimately lead to defects – for example, broken solder contacts, detached bond wires, cracks between the sealing compound for the housing and the semiconductor chip or the metallic base plate. At the same time, moisture reduces the adhesive power of the sealing compound and further increases the risk of cracks. These defects can lead to the failure of not just the element in question, but the entire system. This is where our tests come in. They help us to identify this kind of failure potential at an early stage.
How does this provide added value for researchers and manufacturers of electronic systems?
Stress tests featuring different temperatures and climatic conditions play a key role when it comes to assessing the reliability of products and predicting their service life and are therefore a crucial part of product development. If manufacturers are aware of a system’s weak points, they can incorporate this knowledge into their design, material selection and manufacturing processes before a product goes into series production, ensuring that only products with optimized properties and service lives reach the market. Not only does this save valuable time and resources, it also eliminates the need for expensive product recalls and reduces the number of warranties required, thus boosting customer satisfaction and ultimately the reputation of the manufacturer.
Could you explain in detail how electronic components and modules are tested at Fraunhofer ENAS?
We use various measuring and testing systems to simulate and test the effects of rapid temperature shocks, slower temperature changes and long-term climatic stresses on electronic assemblies. We tailor the temperatures, test durations and number of cycles to which the specimens are exposed based on the future application scenario of the electronic component. We also select the optimum conditions from an industry standard in each case to ensure that the findings obtained are comparable with the existing results.
Our two-chamber shock oven, for example, allows us to subject samples to very rapid temperature changes between -40 °C and 125 °C. This test is important for automotive applications: It simulates a cold start in northern Finland, which presents a particular challenge for electronic assemblies due to the extreme temperatures involved. The amount of time a specimen spends in the cold and hot chambers of our shock oven depends on the volume of the assembly, while the number of test cycles that the electronics must complete is determined by the specific failure modes being investigated in the test in question. By continuously measuring the electrical resistance directly on the component contacts, we can determine the precise time of failure. This is generally indicated by increases in resistance immediately after switching chambers, but it often occurs for a brief moment only. It is possible, for example, for the two sides of a broken contact to close again after breaking, thus restoring the electrical connection. However, if contacts are interrupted in this way, the functioning of the electronics can no longer be guaranteed. Our continuous in-situ measurement can reliably detect these interruptions, even if they only occur briefly. At the end of the tests, we have a set of statistics on the failure behavior of the components. The distribution of the failure times of the individual sample specimens can be used to extrapolate the characteristic service life of the entire product series.
We also have a combined climate/temperature/vibration system which allows us to subject samples to temperature changes, vibrations and moisture levels between 10% and 95% simultaneously while under electrical stress and monitoring. This simulates a wide range of different stresses as experienced by components in their various application scenarios, in which they need to be able to function perfectly in both summer and winter and in foggy, rainy or icy conditions. These combined tests are particularly useful for manufacturers of automotive electronics, machine control systems in the metal and chemical industries and for smart grid applications. Together with manufacturers from these sectors, we are working on new test standards to enable the results to be compared and evaluated on an industry-wide basis.
If we want to reach significantly higher temperatures, we use our high-temperature furnace system which allows us to implement temperature changes from -80 °C to 500 °C. High and rapid temperature changes of this kind are not only relevant to special industrial applications and space travel: New power components for inverters in electric vehicles are made from silicon carbide or gallium nitride rather than the silicon used previously. They can withstand temperatures of up to 300 °C on a long-term basis in regular operation. The accelerated aging process requires them to be tested at even higher temperatures.
With all of the equipment in our test laboratory, we can simulate any climatic environmental influences that electronics may be exposed to, even in extremely challenging applications – from snow and ice in Alaska to the heat of the Sahara. We can subject specimens to temperature, moisture and vibration stresses simultaneously in a very realistic manner in order to find out specifically whether electronic systems can work correctly for as long as intended even in these harsh conditions.
As well as carrying out reliability testing in laboratory environments, Fraunhofer ENAS also performs tests in a more unusual place: namely, deep underground. What exactly does that involve?
We also carry out long-term testing on electronic components for our customers. For this purpose, we set up the European lab for long-term reliability in a former mine. This allows us to perform reliability tests using the natural ambient conditions of the mine with highly energy-efficient temperature changes between 12 °C and 100 °C. The samples are heated to 100 °C in an oven over the course of an hour or so before being cooled by the ambient temperature of the mine over a period of around six hours. After seven hours, the next cycle begins. This corresponds to the typical usage of a vehicle: After a short journey, the vehicle is parked for a prolonged period and remains at a “standstill” for several hours before moving off and driving again. We have been able to carry out these real-life tests, approximating conditions in the field, for more or less the total service life of 15 years that is typical for electronics in automotive, industrial and energy-related applications. These ultra-long-term experiments help us to verify the accuracy of our accelerated lab tests and to improve them further so they can correctly replicate the phenomena of creep fatigue in the various solder and sinter connections on the electronics; for example, with cracks, breakages and delaminations.
Thank you, Ms. Kreyßig, for speaking to us and for sharing these insights into how the service lives of electronic systems are predicted.
If you would like more information about our test services, please feel free to contact us.
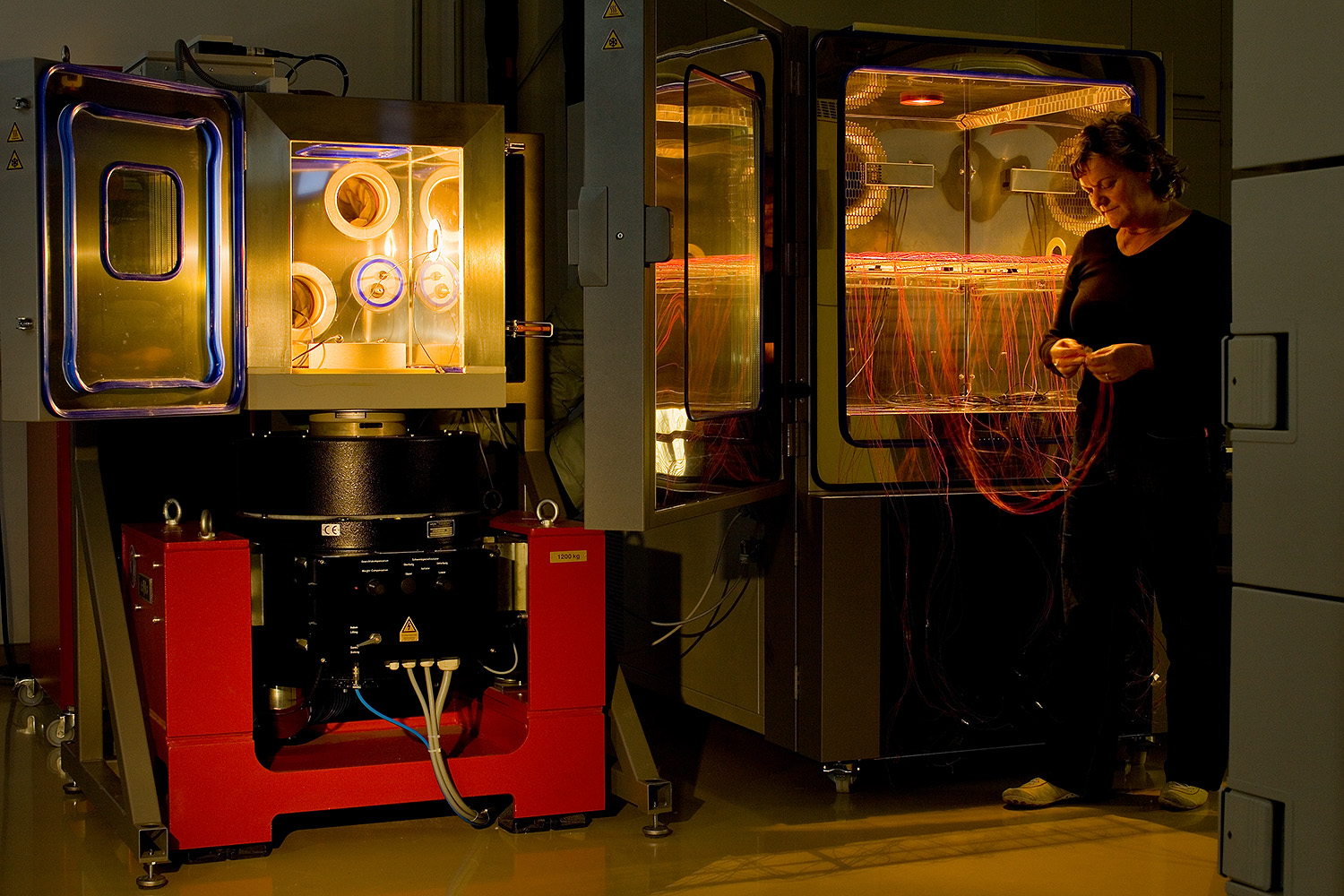
Last modified: