Interview
Allrounder Parylene: Ultradünner Kunststoff mit schützenden Kräften
Wenn Töne und Geräusche immer mehr verschwimmen, die Außenwelt jeden Tag ein kleines bisschen mehr verstummt und Unterhaltungen, vor allem bei lauten Hintergrundgeräuschen, nicht mehr ohne große Kraftanstrengung verfolgt werden können, dann ist eine beginnende Schwerhörigkeit sehr wahrscheinlich. Bleiben diese ersten Anzeichen des Hörverlusts unbehandelt, kann eine vollständige Gehörlosigkeit drohen. Cochlea-Implantate geben hochgradig Schwerhörenden und tauben Menschen Hoffnung, wieder aktiver am Leben teilzunehmen und Zugang zur Welt der Hörenden zu finden. Aktuelle Forschungsbemühungen konzentrieren sich darauf, Fortschritte im Bereich der technisch unterstützten auditiven Wahrnehmung mithilfe von Cochlea-Implantaten zu erzielen, die eine verbesserte Sprachverständlichkeit bei gleichzeitig hohem Patientenkomfort ermöglichen sollen. Innovativer Baustein dieser Entwicklungen ist ein wahrer Alleskönner, der die dafür notwendige Elektronik nahezu unsichtbar schützt: das Polymer »Parylene«. Am Fraunhofer ENAS arbeiten Forschende wie Franz Selbmann daran, sensible Elektronik für die Medizintechnik und Industrie mit diesem hauchdünnen Kunststoff zu versehen und sie damit gegen äußere Einflüsse abzuschirmen. Im Interview erklärt der Wissenschaftler, was Parylene einzigartig macht und welche Anwendungspotentiale das »talentierte« Material zum Beispiel für neue Generationen von medizinischen Implantaten bietet.
Herr Selbmann, am Fraunhofer ENAS erforschen Sie das Material Parylene detailgenau. Können Sie erklären, was genau sich hinter dem Begriff »Parylene« verbirgt und wie das Material hergestellt wird?
Parylene, dessen vollständiger Name Poly(para-xylylene) lautet, ist ein hochinteressantes Material und gehört zu den Polymeren, also den Kunststoffen. Es entsteht durch die sogenannte chemische Gasphasenabscheidung (Chemical Vapor Deposition, CVD). Bei diesem Schichtabscheidungsverfahren wird das Material aus der Gasphase in einer Vakuumkammer bei Raumtemperatur auf unterschiedlichen Substraten, zum Beispiel auf Silizium-Wafer, mit einer extrem dünnen Schichtdicke homogen und spannungsfrei abgeschieden. Die so erzeugte Schicht ist zu 100 Prozent 3D-konform. Das bedeutet, dass auch geometrisch anspruchsvolle Substrate mit außergewöhnlichen Topografien und filigranen Strukturen beschichtet werden können und dabei jede noch so kleine Ecke, jede scharfe Kante, jede winzige Pore und jeder Hohlraum des Ausgangssubstrats komplett und völlig homogen von einer Parylene-Schicht überzogen werden kann.
Was macht das Polymer so besonders und außergewöhnlich?
Das Material verfügt über einzigartige technische Eigenschaften, die es für eine Vielzahl von Anwendungen sowohl für die Medizin, die Elektronik als auch für die Halbleiterindustrie interessant machen.
Vor allem im medizinischen Bereich und in der Gesundheitsbranche wird die herausragende Stärke von Parylene deutlich: Seine Biokompatibilität und -stabilität machen das Material biologisch besonders verträglich, wodurch es für den Einsatz im menschlichen Körper – als Umhausung miniaturisierter Systeme und Hilfsmittel – ideal geeignet ist. Damit entstehen – selbst bei einem dauerhaften Verbleib im Körper – keine pathologischen Wechselwirkungen, es werden keine Allergien, Reizungen oder Abwehrreaktionen ausgelöst und auch in Kombination mit Körperflüssigkeiten werden keine Partikel oder toxischen Substanzen freigesetzt, die sich gesundheitsgefährdend auswirken könnten. Das sorgt für mehr Patientensicherheit und Wohlbefinden.
Das Polymer ist außerdem extrem widerstandsfähig. Da es nicht mit anderen chemischen Stoffen reagiert, also »inert« ist, ist es hervorragend für die Verwendung in rauen Umgebungen geeignet. Dank dieser chemischen Beständigkeit bleibt es auch bei Kontakt mit ätzenden oder aggressiven Reaktionspartnern, wie Säuren, Basen und Lösungsmitteln, völlig intakt und stabil.
Seine Barriereeigenschaften erlauben zudem eine wirksame Abgrenzung beispielsweise verkapselter Elektronik gegen aggressive Umgebungsbedingungen und machen eine Durchdringung von Gasen, Chemikalien oder anderen Flüssigkeiten unmöglich.
Außerdem ist das Polymer dielektrisch. Diese Eigenschaft ist besonders relevant, um elektrisch leitfähige Materialien oder elektronische Bauelemente gezielt elektrisch zu isolieren.
Zu guter Letzt zeichnet sich Parylene durch seine optische Transparenz aus. Das bedeutet, dass Licht ungehindert durch den Kunststoff hindurchdringen kann, was ihn zum Beispiel für Einsatzgebiete in der Optik, wie unter anderem für den Schutz von LEDs, interessant macht.
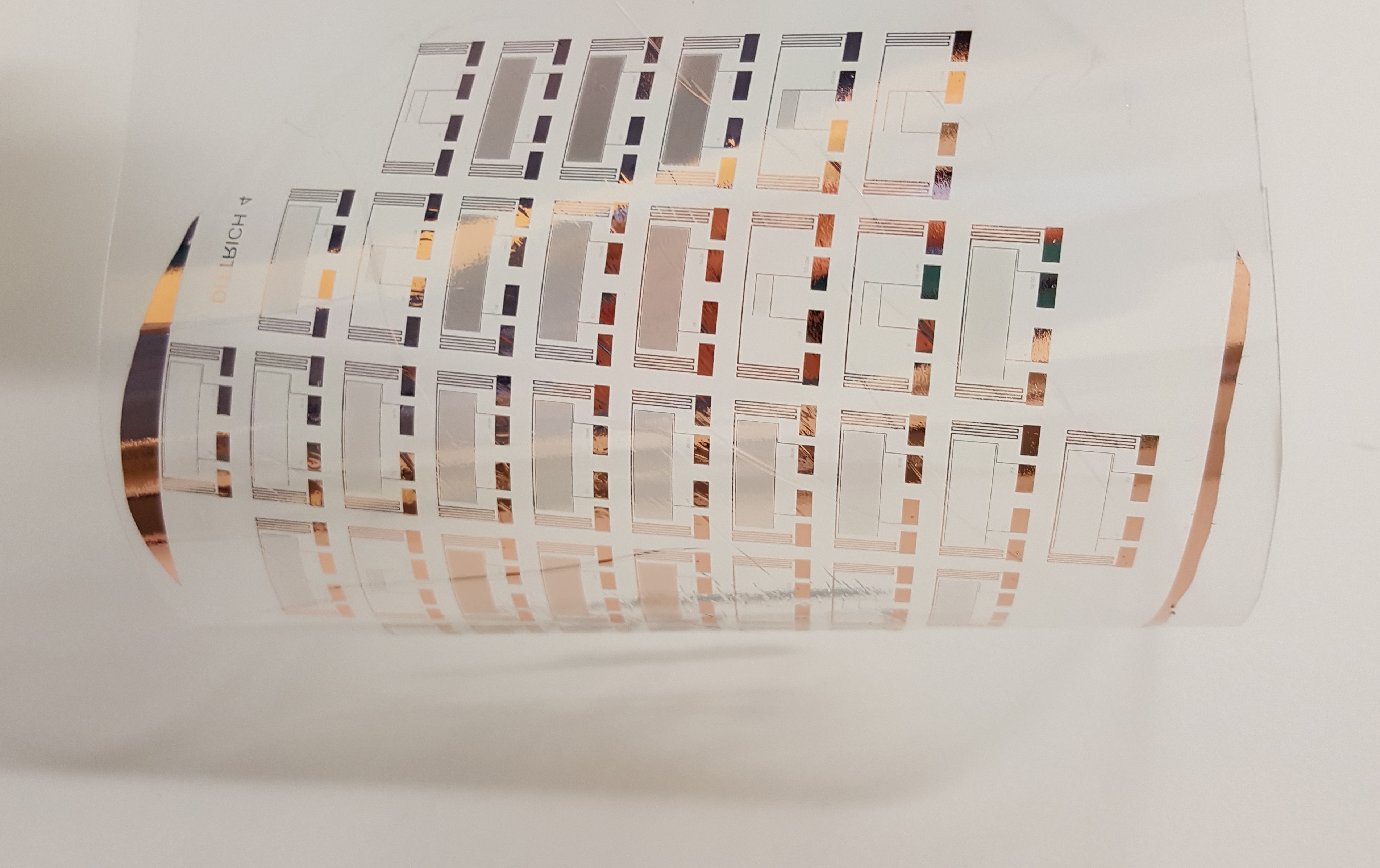
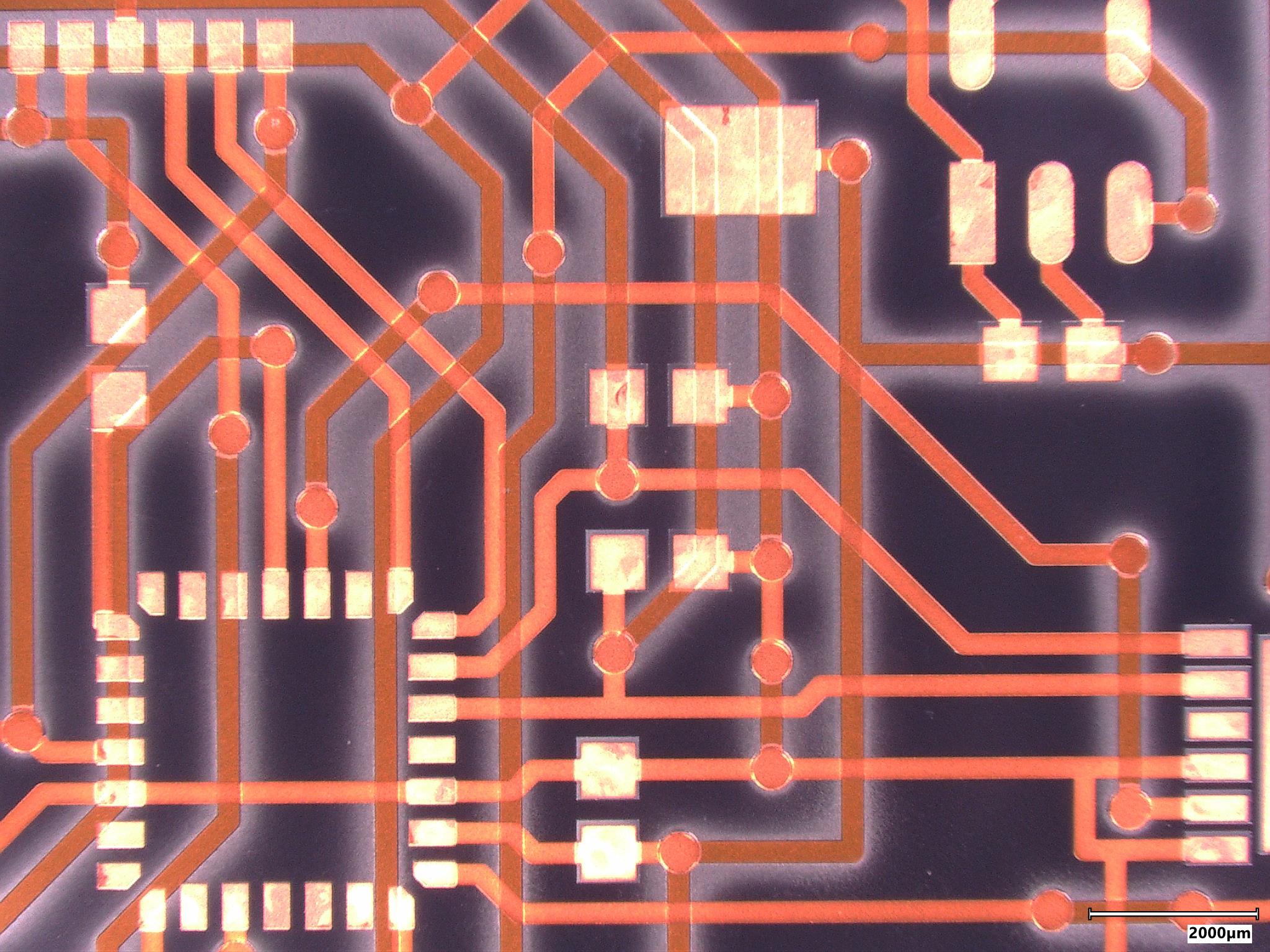
Welche Anwendungsszenarios ergeben sich für das Polymer, in denen diese herausragenden Charakteristika ihre Wirkung entfalten?
Dieses Bündel von Eigenschaften machen das Polymer zum idealen Kandidaten für das Verkapseln, Beschichten, Versiegeln und Veredeln von elektronischen und mechanischen Komponenten und Bauteilen, aber auch von Oberflächen und ganzen Systemen – und das aus den unterschiedlichsten Branchen. Ob im Automobilbau, in der Luft- und Raumfahrt, in der Optik und Mikroelektronik, in der Chemie oder im medizinischen Sektor – in all diesen Bereichen wird Parylene bereits standardmäßig eingesetzt.
Eine der Hauptanwendungen von Parylene stellt das Verkapseln dar, um beispielsweise Leiterplatten mithilfe eines dünnen Parylene-Films mit einem Korrosionsschutz gegen Salz und Feuchte auszustatten und damit die kontinuierliche Funktionsfähigkeit von Systemen zu gewährleisten.
Am Fraunhofer ENAS untersuchen wir außerdem die Eignung von Parylene als Adhäsiv für den Einsatz in mikrotechnologischen Fügeprozessen, in denen das Polymer als haftende bzw. verbindende Bondschicht auf Chip- und Waferebene mit hoher mechanischer Festigkeit verwendet werden kann. Da der Kunststoff sehr temperaturbeständig ist und damit auch höheren Temperaturen Stand hält, konnte er im Bereich der Aufbau- und Verbindungstechnik in der Mikroelektronik und Mikrosystemtechnik bereits erfolgreich eingesetzt werden, um ein neues und Parylene-basiertes Bondverfahren zu etablieren.
Außerdem erforschen wir, wie sich auf Basis von Parylene ultradünne, flexible Leiterplatten realisieren lassen. Der Kunststoff wird hierzu auf einem Wafer abgeschieden und mit Leiterbahnen aus Metall versehen. Mit einer Dicke von 20 Mikrometern ist die so entstehende Parylene-basierte Leiterplatte um den Faktor 10 dünner als bisherige kommerziell verfügbare Leiterplatten. Auf diese Weise lassen sich nah am Körper getragene Wearables herstellen, zum Beispiel in Form medizinischer intelligenter Pflaster, mit denen Vitalparameter kontinuierlich überwacht werden können. Anwendungspotential sehen wir beispielsweise auch im Bereich der »geometrieadaptiven Sensorik« und beim Überwachen von Leichtbaustrukturen. Derartige ultradünne Parylene-basierten Leiterplatten könnten als Träger entsprechender Sensoren zum Beispiel in die Tragflächen von Flugzeugen integriert werden und so sensible Parameter überwachen, die Hinweise auf Materialermüdung und Verschleiß geben. Das geringe Eigengewicht der Sensorik beeinflusst die Statik und Stabilität der Flugzeug-Tragflächen dabei nicht. So ließen sich Materialien vorausschauend austauschen noch bevor eine gravierende Gefährdung eintritt.
Sie sprachen davon, dass Parylene biokompatibel ist, was es für Einsatzgebiete vor allem im medizinischen Bereich attraktiv macht. Welche konkreten Einsatzgebiete sehen Sie im Gesundheitssektor?
Schlägt beispielsweise das Herz von Patientinnen und Patienten nicht mehr im richtigen Takt, kann ein Herzschrittmacher notwendig werden, damit es wieder in den richtigen Rhythmus zurückfindet. Diese bestehen häufig aus einem Titangehäuse, welches die notwendige und sensible Elektronik trägt. Der Einsatz von Parylene, das die gesamte Elektronik als Schutzschicht ummantelt und verkapselt, könnte ein Titangehäuse überflüssig machen und würde damit Möglichkeiten zur weiteren Miniaturisierung von Herzschrittmachern und anderen medizinischen Implantaten die Tür öffnen, die dadurch deutlich kleiner und leichter als bisherige Systeme werden.
Manche Patientinnen und Patienten bemerken zudem nach dem Einsatz eines Herzschrittmachers in den Körper eine leichte »Ausbeulung« der Haut am Implantationsort, welche durch das Titangehäuse entsteht. Ein Parylene-verkapseltes System, das sich besser an den Körper anpasst, würde für mehr Tragekomfort sorgen.
Parylene-basierte Ummantelungen und Verkapselungen von Elektronik bieten nicht nur für Herzschrittmacher enormes Potential, sondern auch für gänzlich neue Generationen von medizinischen Implantaten, die perspektivisch ohne zusätzliche Gehäuse auskommen. Wie das eingangs beschriebene Beispiel zeigt, sollen mithilfe von Parylene Fortschritte im Bereich der Hörprothetik erzielt werden. Woran arbeiten Sie genau?
Gemeinsam mit verschiedenen Partnern arbeiten wir im Zukunftscluster »SEMECO« daran, Cochlea-Implantate zukünftig nicht nur kleiner und leichter, sondern auch intelligenter zu machen und damit schwerhörigen oder ertaubten Patientinnen und Patienten wieder Hoffnung auf mehr Lebensqualität zu geben. Dabei sollen Signale der Gehirnaktivitäten, die als Indikator für Aufmerksamkeit, Wahrnehmung und Sprachverständnis dienen, erfasst werden, um auf deren Basis das Implantat individuell anzupassen. Auf diese Weise ließen sich Störgeräusche unterdrücken, während zugleich der auditive Fokus auf bestimmte Geräusche, zum Beispiel von Gesprächspartnern, gerichtet wird.
An unserem Institut entwickeln wir im Rahmen dieser Forschungsarbeit auf Basis von Parylene eine hochminiaturisierte und biokompatible Verkapselungsmethode für das Implantat. Durch die Kombination verschiedener Schichten soll eine »Ultrabarriere« entstehen. Diese soll nicht nur die integrierten Sensoren und Komponenten des Innenohr-Implantats vor Körperflüssigkeiten schützen, sondern auch den menschlichen Organismus vor Schadstoffen aus dem technischen System bewahren. Hinzu kommt, dass die Schichtkombination als elektromagnetische Abschirmung für die empfindlichen Hochleistungsschaltkreise fungiert und so optimalen Schutz garantiert, ohne auf ein herkömmliches Gehäuse angewiesen zu sein. Durch den Einsatz von Parylene kann das komplexe Implantat damit deutlich verkleinert werden, was die Einbringung in den Körper überhaupt erst ermöglicht und dem Ziel dient, den Patienten- und Tragekomfort zu verbessern.
Herzlichen Dank, Herr Selbmann, für dieses Gespräch und die Einblicke in den »Alleskönner« Parylene.
Wenn Sie weitere Informationen zum Thema Parylene wünschen oder Fragen zu den vielfältigen Einsatzgebieten des Kunststoffes haben, dann kontaktieren Sie uns gern.
Letzte Änderung: