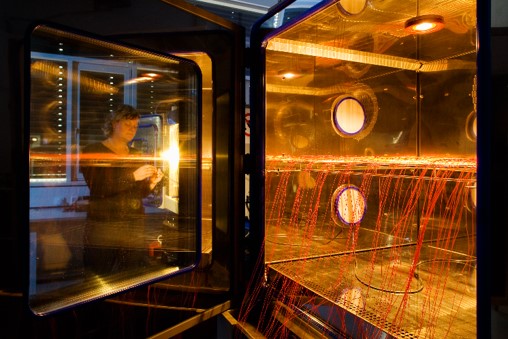
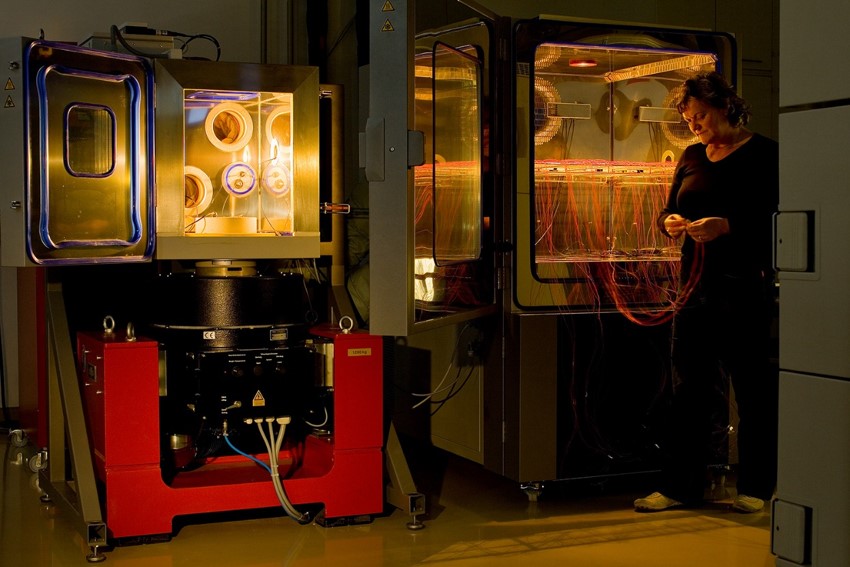
Eine sachkundige Prognose der Zuverlässigkeit von Gesamtsystemen der Mikro- und Nanosystemtechnik kann zeitaufwendige Iterationen im Aufbau von elektrischen Systemen vermeiden und innerhalb der Entwicklungsphase eventuell vorhandene Schwachstellen aufzeigen. Das Abschätzen der charakteristischen System-Lebensdauer aus dem Zuverlässigkeitsverhalten der kritischen Komponenten des Systems macht dies möglich. Das Prüfen des Komponentenverhaltens unter systemrelevanten Bedingungen liefert dazu die erforderlichen Informationen, welche nachfolgend geeignet verknüpft und bewertet werden.
Die Arbeitsgruppe 'Lebensdauerbestimmung' widmet sich dieser Forschungsaufgabe durch experimentell dominierte Lösungsstrategien. Basierend auf mehr als 25 Jahren Erfahrung im Prüfen der thermo-mechanischen Zuverlässigkeit elektronischer Komponenten und Systeme erforschen wir in enger Kooperation mit zahlreichen Partnern aus der Industrie neue Methoden für die
- beschleunigte Prüfung der thermo-mechanischen Zuverlässigkeit für neue Technologien (z.B. SiC- & GaN-Bauelemente, Ag- & Cu-Sintern)
- multimodale Belastung (passive und aktive Temperaturwechsel, Temperaturwechsel und Vibration, Feuchteeinfluss) zur realitätskonformen Ermittlung der Komponenten-Lebensdauer für die neuen Anwendungen mit komplexen Beanspruchungsprofil (Elektromobilität, automatisches Fahren, Industrie 4.0, Smart Grid, Smart City, etc.)
Auf dem Gebiet der Lebensdauermodellierung leisten wir Beiträge zur Erweiterung der Methodik für
- das Bestimmen von Beschleunigungsfaktoren zwischen verschiedenen Lebensdauertests sowie gegenüber dem Betriebsverhalten
- die Aggregation und die summarische Bewertung der Zuverlässigkeit unter Realbedingungen, d.h. bei sehr unterschiedlichen Belastungen
- das Abschätzen der Systemzuverlässigkeit aus dem Verhalten der Einzelkomponenten unter Einbeziehung irreversibler Ausfallmechanismen
Durch die analytische Prüfung und Charakterisierung (Gruppe Analytik und Charakterisierung) realer Komponenten im Zusammenhang mit der Lebensdauerbestimmung können die Degradationsvorgänge phänomenologisch aufgeklärt und quantitativ präzise analysiert werden. Sie bildet somit das Fundament für die Arbeiten zur Modellierung und Simulation.