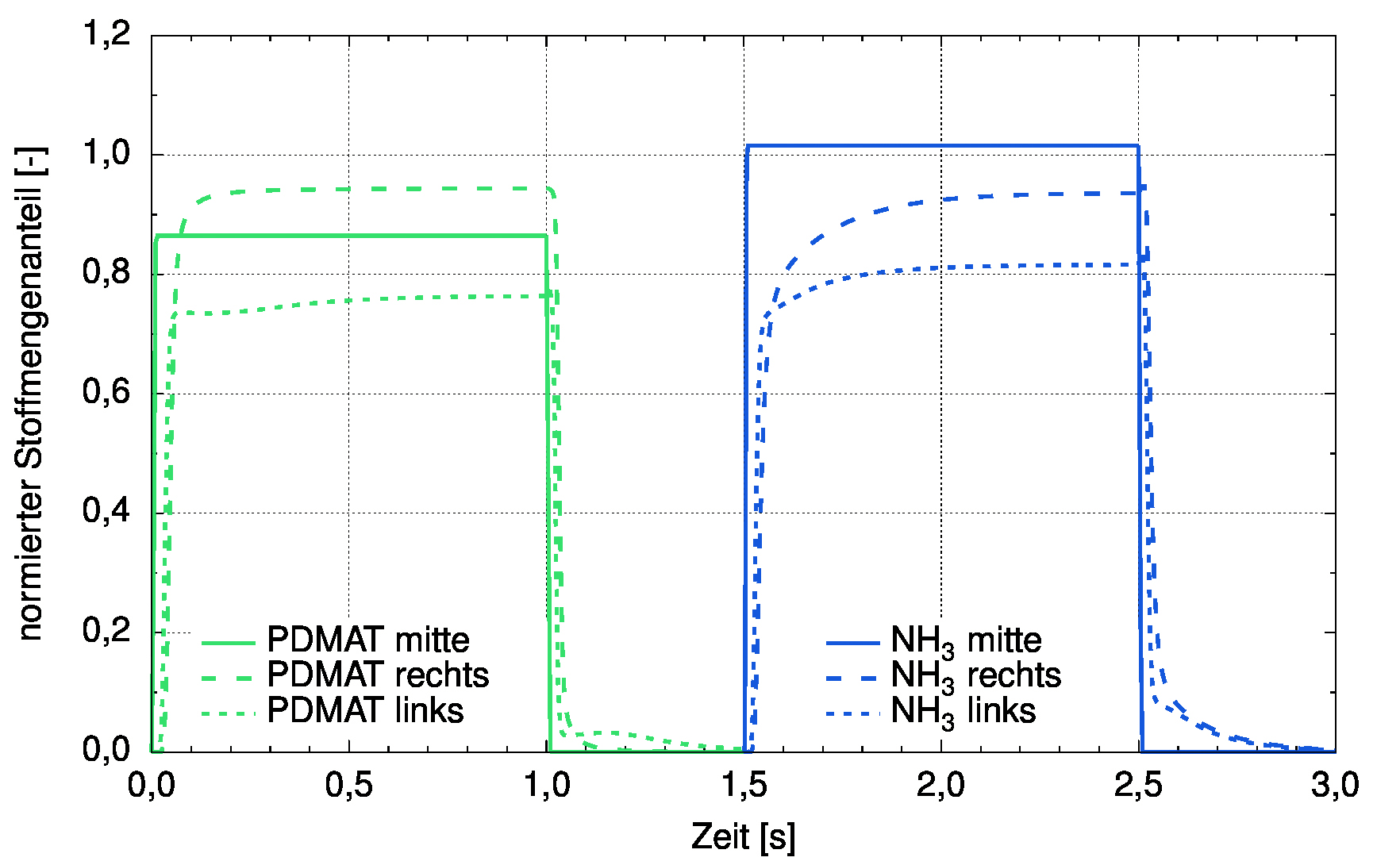
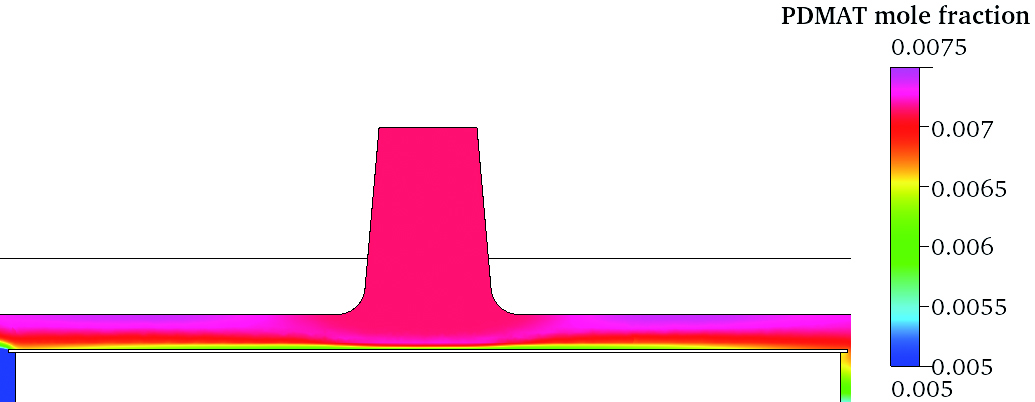
Die fortschreitende Miniaturisierung mikroelektronischer Bauteile führt zu einer steigenden Nachfrage nach Abscheideverfahren zur Erzeugung von gleichmäßigen, homogenen und extrem dünnen Schichten. Die Atomlagenabscheidung (ALD) besitzt die Fähigkeit zur Abscheidung dieser Schichten selbst in Strukturen mit großen Aspektverhältnissen. Im Rahmen des Projektes EVOLVE mit dem Chiphersteller GLOBALFOUNDRIES, dem Fraunhofer IPMS-CNT und der TU Dresden haben wir einen TaN-ALD-Prozess für die Fertigung von Kupferdiffusionsbarrieren untersucht. Mithilfe der Reaktorskalensimulation analysierten wir die Precursorverteilung während der Dosier- und Spülschritte in einem Einzelwaferreaktor. In der Simulation zeigte sich eine verringerte Präkursorkonzentration direkt über dem beheizten Wafer. Durch die Temperaturdifferenz zwischen dem beheizten Wafer (200 °C) und dem kälteren, einströmenden Gas (90 °C) ergibt sich ein starker Temperaturgradient über dem Wafer. Dieser Temperaturgradient verursacht Thermodiffusion, wodurch das größere Gasmolekül (Precursor) von dem heißen Bereich (Wafer) weg diffundiert. Mittels Reaktorskalensimulation konnten wir somit Einblicke in das Strömungsfeld und die Precursorverteilung innerhalb des Reaktors erhalten, was anders nicht möglich wäre. Basierend darauf kann mit dem Projektpartner eine weitergehende Prozessoptimierung erfolgen.