News
Fail-safe monitoring: Energy self-sufficient sensors look ahead to keep track of infrastructures
Working in collaboration with the universities in Chemnitz, Paderborn and Bochum, a German research team from Fraunhofer ENAS has succeeded in developing an innovative sensor concept that operates independently of external power sources and generates the energy it needs by itself. The miniaturized, compact sensor technology creates the conditions to monitor industry, building and transportation infrastructures continuously and with long-term stability and to optimize maintenance cycles. The unique combination of a piezoelectric element and a memristor enables shocks and vibrations to be detected and potential risks to be uncovered at an early stage. This allows both failure times and downtimes to be minimized and unnecessary costs to be avoided.
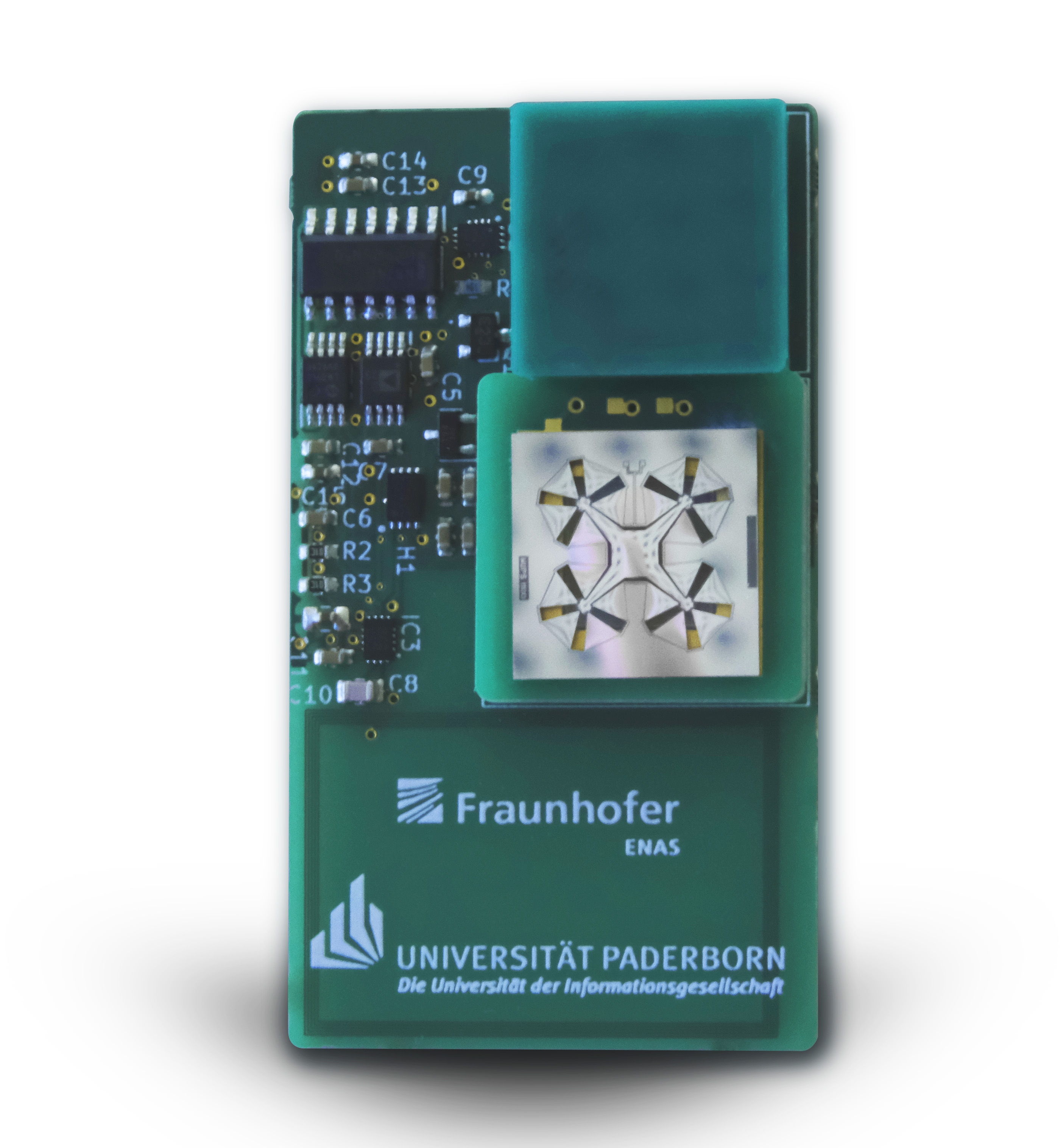
Historic buildings, sensitive transportation goods and industrial machinery – on a daily basis, these are all subjected to vibrations and shocks that are caused by external environmental influences, such as traffic noise, transport-related shocks and vibrations during operation, and that lead to wear and material fatigue. Over the long term, mechanical stresses of this nature can cause cracks in buildings and freeway bridges or result in entire industrial plants failing. Permanent sensory monitoring is therefore essential in order to reliably maintain the functionality of infrastructures and ensure safety.
“This type of close, permanent monitoring typically requires hundreds of sensors and hundreds of thousands of kilometers of cables, taking up human resources and giving rise to huge costs. In addition, electrical auxiliary energy in the form of batteries, for example, is needed to operate current wireless sensor solutions. These batteries have to be serviced at regular intervals and replaced preemptively in order to guarantee that the sensors function perfectly at all times. This also creates a huge environmental problem, as batteries often contain toxic substances that can be harmful to nature when they are disposed of,” says Dr. Sven Zimmermann, Head of the Group “Nano Devices/PVD,” at Fraunhofer ENAS explaining the motivation behind the development.
Self-sufficient system: The sensors cover their own energy needs
The researchers have been working on a solution to the above problem and have developed an energy self-sufficient microsensor system that works entirely without batteries or cables and that generates its energy exclusively from the measured variable. In this concept, the transducer is simultaneously the energy supplier.
At the heart of the new solution are two microtechnological components: One is a piezoelectric converter measuring around 2 x 2 centimeters that detects mechanical movements such as vibrations and shocks and converts the mechanical energy into electrical energy. “This energy is enough to continuously collect data from critical harmful events, such as those that indicate possible wear to components, and to store this data on a memristor. At up to 600 nanometers in size, the memristive cell is some orders of magnitude smaller than the tiniest batteries, yet it has enough memory capacity to reliably store a large amount of information over long periods,” says Dr. Sven Zimmermann.
Perfect memory: memristor stores information without limitations
With their “zero-energy” solution, the researchers are surmounting the challenges presented by current, commercially available sensory monitoring systems that operate with external energy sources or energy harvesting concepts. In those systems, an interruption to the power supply will sooner or later result in all the generated data being lost, meaning that it will no longer be possible to evaluate critical parameters.
This shortcoming is overcome by the memristor as a nanoionic storage medium. “Memristors have an interesting memory effect: If current flows through them, they change their resistance. These changes in resistance are not only stored non-volatile, but can also be evaluated precisely. Even if no current is flowing, the data is retained and can be read out and reset with an NFC-enabled end device such as a standard smartphone,” the Fraunhofer expert explains.
From acute hazard elimination to predictive maintenance
The data that is read out maps mechanical load patterns and provides information on the duration and number of physical events, shocks and vibrations, that have acted upon industrial plants or buildings, for example. Experts can use this long-term monitoring and the collected signals to draw valuable conclusions on the structural condition of machinery, for instance, and to assess whether mechanical components need to be replaced. As a result, it is possible to plan ahead for maintenance rather than base it on defined time periods. In addition, defective components can be replaced preemptively in good time, before a harmful event even occurs, preventing possible machine downtimes caused by wear or material fatigue and avoiding the time and costs involved in fixing such issues.
An unlimited range of applications for “zero-energy” sensors
In addition to applications in industrial settings and in the fields of mobility and transportation, the scientists also envisage that their sensor solution could provide new approaches for optimizing how things are done in the logistics and architecture sectors: “For example, fragile cargo needs to be transported safely from one place to another without being damaged. Sources of stray acoustic radiation in historic buildings cause damage to the building structure over the long term and regular structural tests have to be carried out. In these scenarios, a permanently operating sensor can deliver valuable, traceable data and enable changes in the condition of buildings or products to be measured. Applied to a flexible substrate, the sensor is also almost invisible, and its low weight means it does not affect the properties of components or infrastructures,” Dr. Sven Zimmermann explains. These advantages will in future allow applications to be addressed that – until now – have not been able to be monitored due to unfavorable structural conditions regarding routing wiring harnesses or sequential battery replacements.
A German research partnership: the “UpFUSE” joint research project
The innovative sensor system is the result of a close cooperation between Chemnitz University of Technology, Ruhr University Bochum, Paderborn University and Fraunhofer ENAS in Chemnitz. The sensor technology has been developed as part of the four-year “UpFUSE” project, which has been funded by the German Federal Ministry of Education and Research (BMBF), together with industry partners. The aim of the project was to explore passive wireless sensor systems for energy self-sufficient shock and vibration monitoring.
Last modified: