Fraunhofer ENAS presents a gyrocompass for indoor applications and a monitoring system for power distribution networks at SENSOR+TEST digital 2021
At the digital SENSOR+TEST 2021, Fraunhofer ENAS presents a monitoring system for condition monitoring of plug and cable connections in switching gears for power grids and a MEMS based gyrocompass.
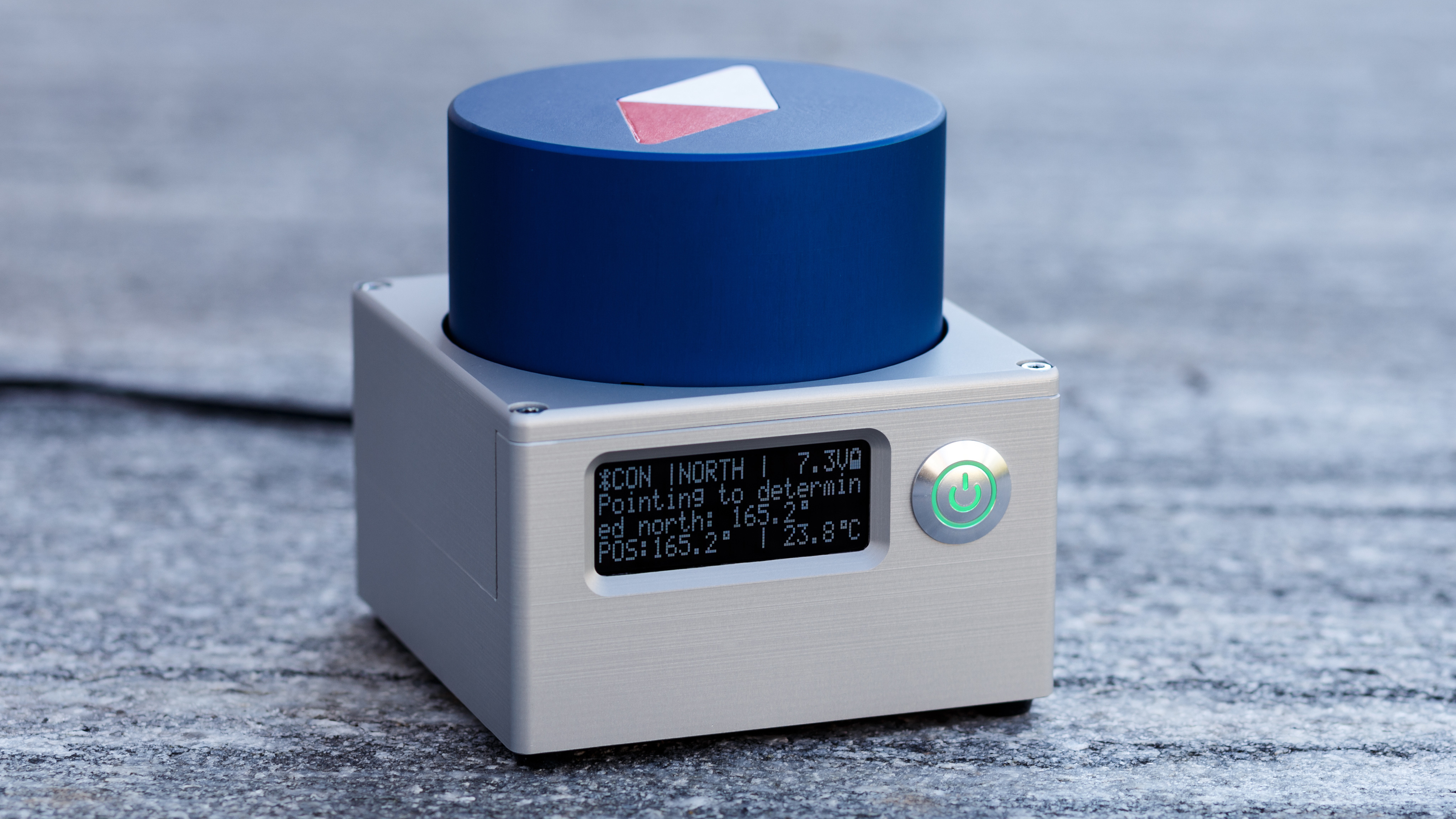
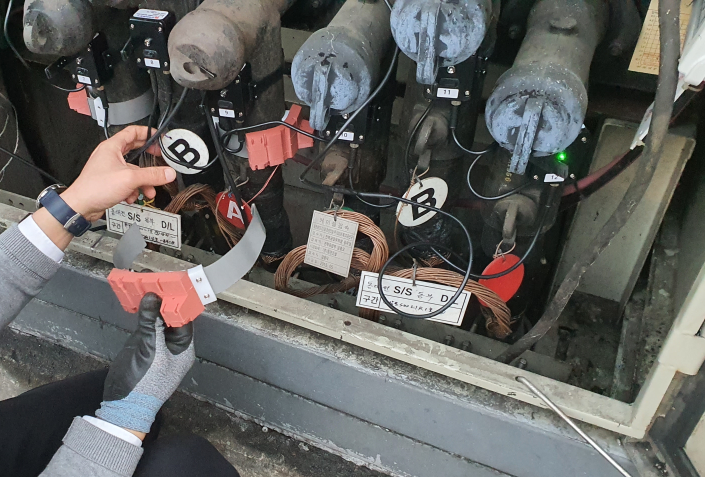
The SENSOR+TEST measurement fair takes place as a digital trade show from May 4-6, 2021. This year, the Fraunhofer Institute for Electronic Nano Systems ENAS is represented as an online exhibitor and presents technologies, components and systems developed at the institute from the world of sensor and measurement technology. Among other things, the research institute shows how MEMS gyroscopes are used in a gyrocompass and how power distribution grids can be monitored using a multi-sensor system for cable connections.
Compass based on a MEMS gyroscope
Nowadays north-finders based on gyroscopes are used because of their robustness against local Earth magnetic field distortion and independence of electromagnetic transmission. Furthermore, the systems can be used to align equipment in reinforced concrete buildings that requires a specific orientation to the Earth’s rotational axis.
The high resolution and precision needed for north-finders is currently only achieved by optical gyroscopes or hemispherical resonator gyroscopes. But they are much more expensive and larger than state-of-the-art MEMS gyroscopes.
Fraunhofer ENAS designed an easy-to-use, compact, transportable, standalone north-finder based on one MEMS gyroscope. The in-house developed, fully integrated tuning fork MEMS gyroscope offers low enough noise and drift to determine north heading down to 1 degree of deviation in less than 10 minutes at a latitude of 50.8 degrees (Chemnitz, Germany) without additional signal conversion electronics. The build in sensor has a bias instability of 0.63 °/h and a noise floor (angular random walk, ARW) of 0.02 °/√h. Moreover, the implemented Maytagging algorithm allows the use of inexpensive consumer electronics, for example a standard stepper motor and low-cost microcontrollers. The measurement routine is fully controlled by the microcontroller, which also collects the angular rate data and determines the north direction by phase fitting. The power consumption stays below 4 watts for the complete measurement cycle.
The gyrocompass will be presented in a short presentation at the Digital Agenda on Tuesday, May 4 at 9 a.m.
Monitoring system for the cable connections of cable-based power grids
The flexible, easily mountable, small-sized, self-sufficient multi sensor wireless monitoring system for medium voltage cable joints was developed together with an international grid operator. With the help of this real-time monitoring system, faults in the cable connections of cable-based power grids can be detected at an early stage, appropriate maintenance work can be carried out and blackouts avoided. In addition, the developed measurement system can contribute to the large-scale digitization of the distribution network. This enables the network operator to continuously record data on power consumption, critical conditions or incipient faults.
The individual sensor nodes consist of a wireless communication module, a power conversion module, and various sensors for detecting e.g. partial discharge, over-temperature and external impacts such as vibrations or shocks. The developed system is featured by an impressive flexibility, small size and small weight. It can be fitted easily around all common power cables with shielding and cable joints. Even the current induction energy harvester has a flexible design. From a current flow of around 15 amperes, the radio electronics and sensor technology is supplied with sufficient energy. The whole sensor node including radio, sensors and energy harvester is designed for and practically tested in a wide operating temperature range from –40°C to +110 °C. The system is currently undergoing extensive field testing in a switchgear in a 22.9 kV distribution grid.
Last modified: