CNT based force sensors: Process Monitoring in forming tools
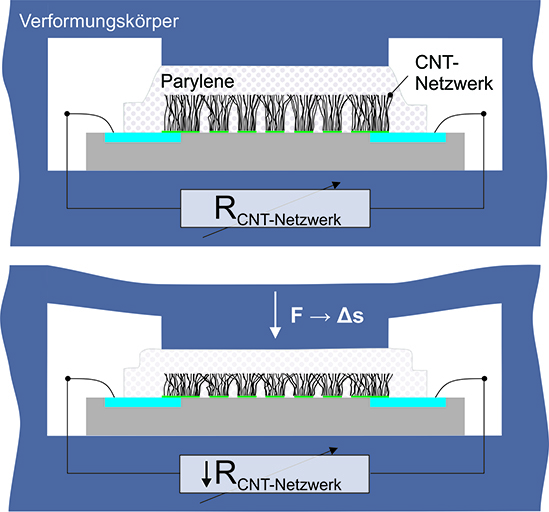
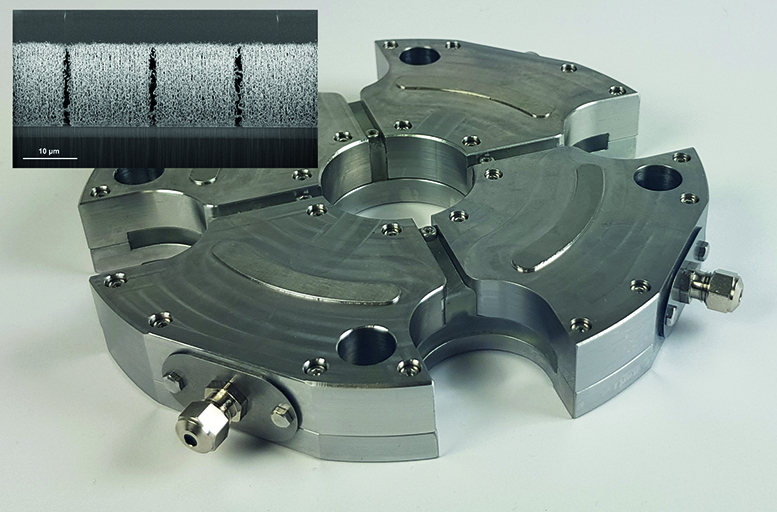
For precise process monitoring of cutting and forming processes a vicinity of the sensor system to the working point is necessary to determine the real forces in machine tools. This vicinity of the working point requires a high sensitivity of the sensors to obtain a high stiffness of the sensor environment. A to large stiffness loss due to the integrated sensors would lead to an accuracy decrease of the components and to a degradation of dynamic properties of tools and machines.
To satisfy these requirements a novel force sensor was developed. The sensor principle is based on a network of vertically aligned carbon nanotubes (CNTs) which electrical resistance can be altered by compression.
For realizing a load cell, CVD-grown CNT structures were arranged as resistors in a Wheatstone bridge configuration and integrated in a deformation element. For process monitoring a sensor cell with four testing points in a circular arrangement was developed. Following results could be obtained from testing the load cell in a press test stand:
- For normalized load until nominal load, a sensitivity up to 75 mV/V could be achieved. This is 35 times higher as it is the case for standard metallic strain gauges with 2 mV/V sensitivity.
- The deformation element has a stiffness of 8 kN/µm. Comparable commercial available force sensors with nominal load between 1 and 5 kN have a stiffness from 0.05 to 0.2 kN/µm. Therefore, the stiffness of the CNT sensors is one to two orders of magnitude higher.