Monolithically integrated 2D magnetic field sensors based on GMR spin valves
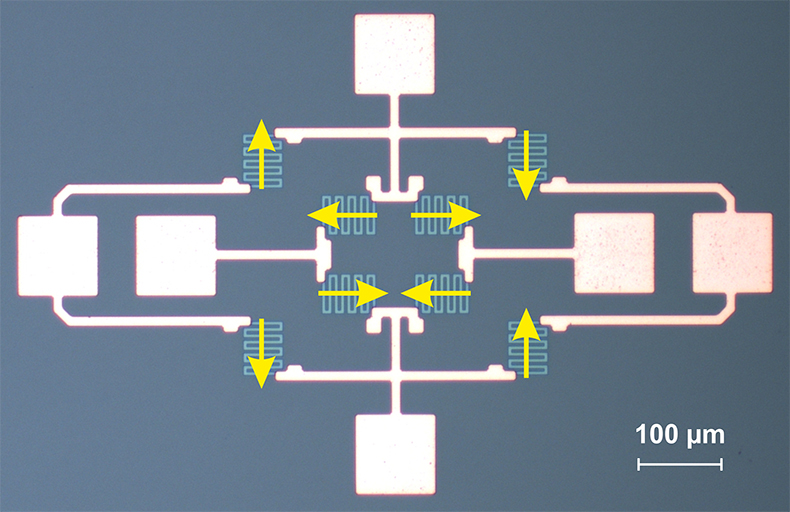
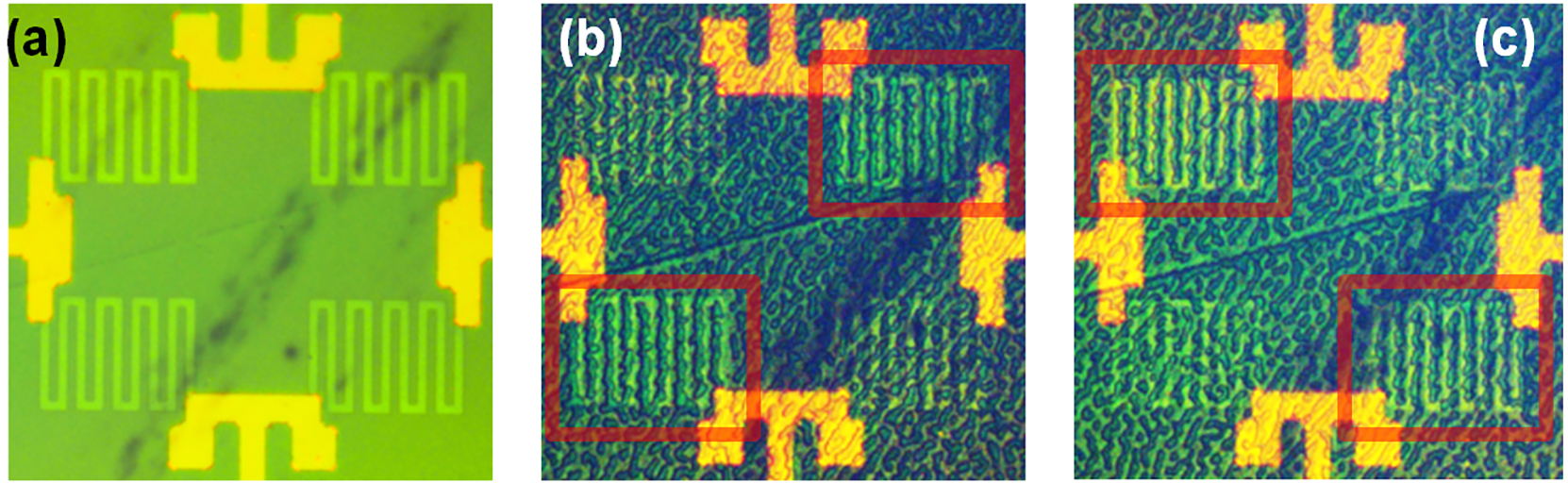
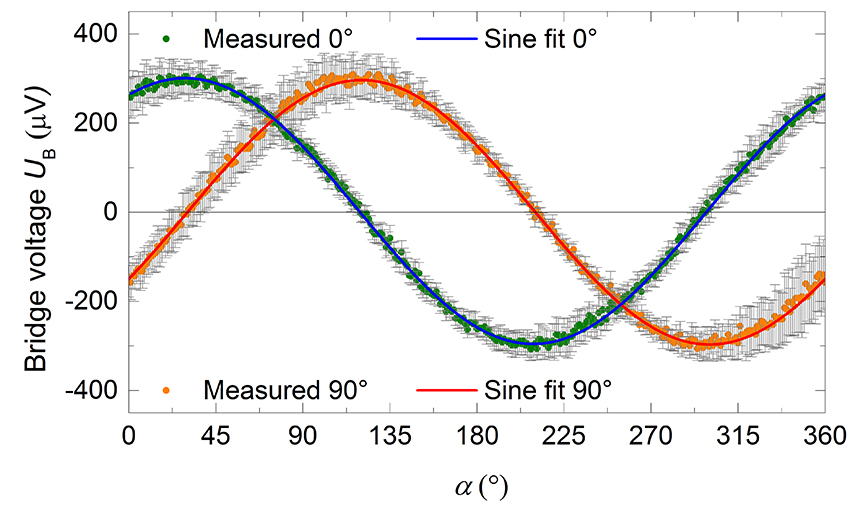
Magnetic field sensors have become omnipresent in everyday life. Being free of wear and small in size, they prove indispensable in a vast variety of mechatronic and electronic devices. For instance, they are used in large numbers in every modern car for providing precise information on the position of doors and steering units or on the rotation speed of wheels and shafts. They also serve as contactless gauges for electric currents. The sensors thereby often work under challenging operating conditions, such as elevated temperature or reactive atmospheres.
Magnetic field sensors are also prominent as built-in components of smartphones: Possessing multi-dimensional sensitivity there, they serve as electronic compasses for precise navigation by means of the geomagnetic field. For this specific application it becomes apparent that not only the measurement of the pure magnitude of a magnetic field, but also the detection of its direction is imperative. Classically, three independent Hall sensors were employed for such purposes. However, the ever-growing demands for further miniaturization, energy efficiency as well as accuracy and precision have paved the way for the superior magnetoresistive sensor technology. The giant magnetoresistance (GMR) effect (Nobel Prize for Physics in 2007) as applied in so-called spin valve sensors represents one of the market-leading technologies.
We have designed and manufactured 2D GMR spin valve sensors in an innovative and cost-effective monolithic integration. For this, the entire sensor device is fabricated from the very same piece of wafer by means of a specific laser-based post-processing step for magnetic patterning. As sensor materials, we use partially exchange-coupled metallic nanolayers and structure them in the form of centred double full Wheatstone bridges of meanders by plasma etching, see figure 1. For a maximum signal-to-noise ratio, an antiparallel alignment (“pinning”) of the magnetic axes of neighbouring bridge meanders is accomplished. In addition, the axes of the two nested bridges must be rotated by 90° relative to each other for providing 2D sensitivity, cf. figure 1. Together with our partner Laserinstitut Hochschule Mittweida, we have successfully established this precise magnetic micro-patterning process by laser modification. The resulting magnetic structure can be visualized by magneto-optical microscopy, see figure 2.
We further optimized the sensors characteristics in terms of maximum signal sensitivity and minimum hysteresis: By experiments and micromagnetic simulations we systematically studied how the geometry (stripe width, length, U-turns, total length, …) of the constituent single meanders influences the total magnetic structure and the electronic response. Moreover, we investigated the impact of pinning orientation and shape anisotropy on the sensor sensitivity.
Applying the best suited meander geometry obtained by our research, we eventually demonstrated that the developed 2D sensors can readily be employed for determining the magnitude and the direction of small magnetic fields with high spatial (~1 mm) and temporal (~1 ms) resolution.