bioElektron - bio-degradable electronics for active implants
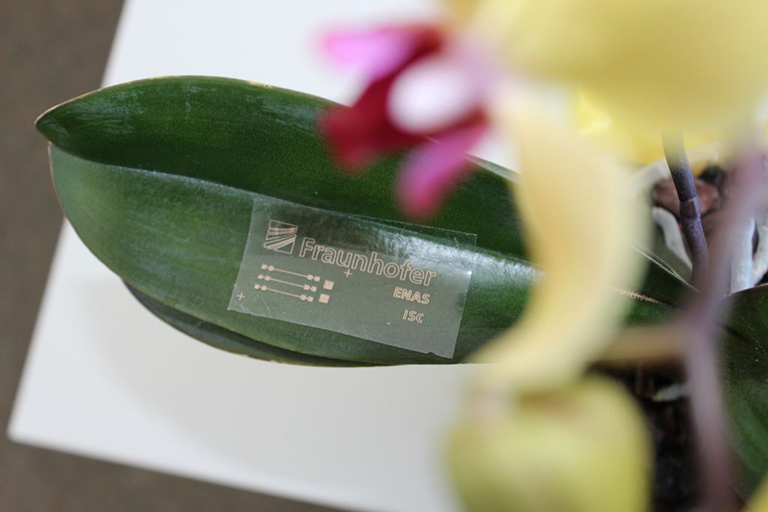
Surgeries are always a severe intrusion into the human body. In some cases there are at least two required: The first one to implement an electrode for interaction and the second one to remove it after use. Based on this scenario it would be handy if all material that is needed remains in the body and is degenerated. For this use case, the Fraunhofer Institutes ENAS, IBMT, ISC and IWKS, led by Fraunhofer FEP, choose, develop and evaluate a suitable set of materials for their application as electrodes, which work for a defined period of time before they are bio-absorbed in the body. Furthermore, also an in situ amplification of signals is under consideration, employing transistors built of zinc or polymeric materials that are also degraded by the body after its use.
At Fraunhofer ENAS, all bio-degradable printed passive and active microelectronic components were deposited using inkjet and aerosol jet technology with adapted post treatment technologies in order to acquire future solutions for medical implants. The aim of these printed electronic implants is to generate stimulation or impulse within a human body, to unleash certain hindered actions. The implementation of digital manufacturing tools such as inkjet and aerosol jet technology endorses tunable and precise deposition of bio-degradable functional materials such as conductors, dielectrics and semiconductors for building devices with predictable performance. Hereby, synergies within digital fabrication are used by exploiting complementary printing capabilities of different printing technologies in order to compensate rheologic differences within used ink systems formed by particle size distribution or viscosity within the printing process itself.