Reliability assessment and optimization of a smart drive unit
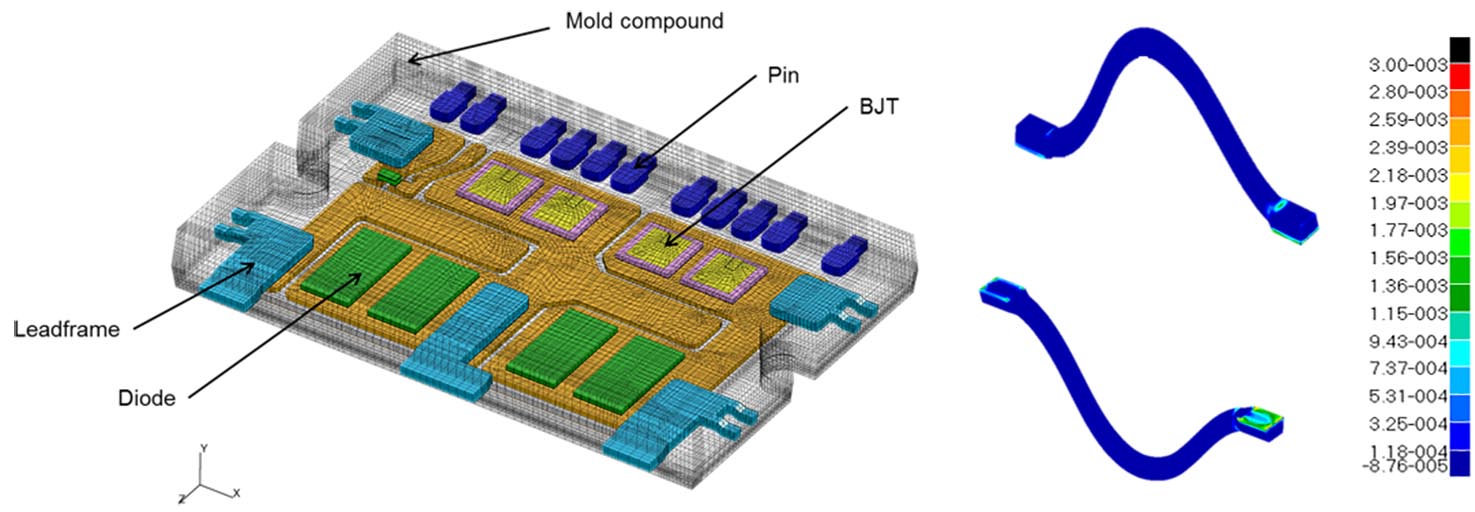
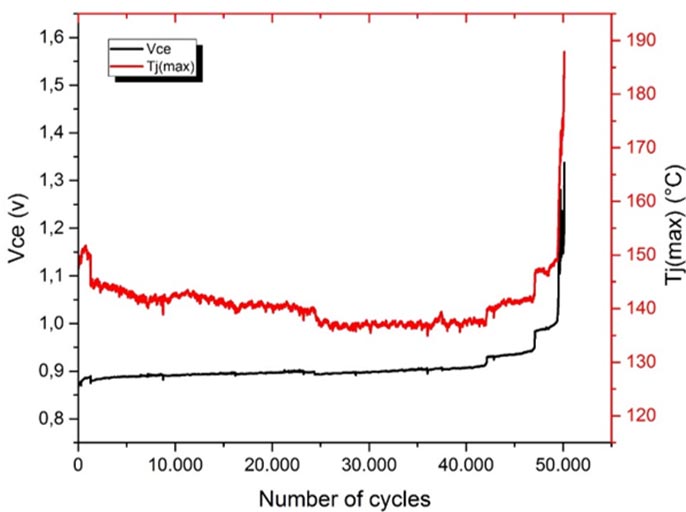
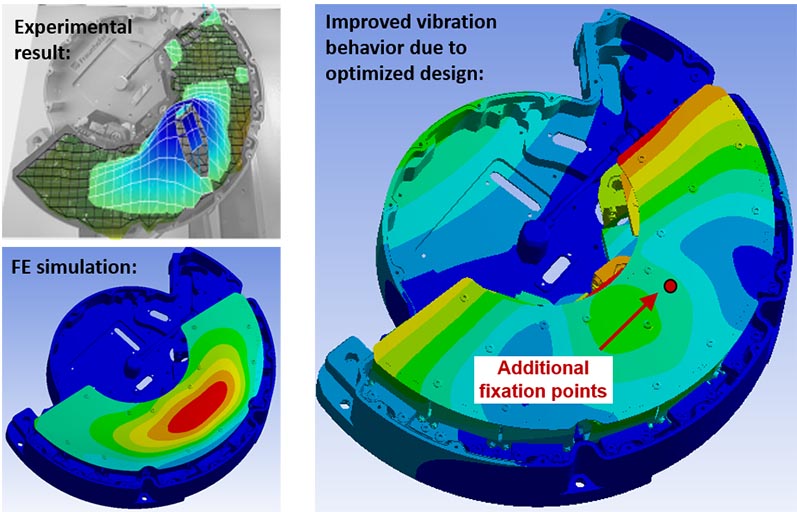
The requirements for commercial vehicles as well as for construction machines in terms of performance, efficiency and reliability (uptime) are constantly growing. These challenges have been addressed within the European project COSIVU (grant agreement no. 313980) by developing a novel electric drive-train architecture for construction vehicles as well as for passenger cars. The main features of the developed system are high modularity, compactness and efficiency (up to 50 % less power losses than in conventional systems). They have been achieved by a highly sophisticated mechatronic integration of electric motor, power electronics (featuring full SiC bipolar junction transistors and diodes), cooling system, and control electronics. Furthermore, health monitoring features such as thermal impedance monitoring for the SiC power modules as well as structure-borne sound analysis for the e-motor and gearbox have been implemented.
In order to enable subsequent commercialization of the developed systems after the course of the project, reliability investigations have been carried out along the development process. The focus has been set on two topics which have been identified as being potentially critical and which will be described in the following.
Reliability investigations on SiC BJT power modules
Main subject of investigation was the newly developed SiC bipolar junction transistor (BJT) power module. In order to identify potential weak points and to assess the reliability of the new technology, thermo-mechanical FE simulations in combination with warpage measurements and thermal analyses (for calibration purposes) have been performed (Fig. 1). In parallel, power cycling tests on the new SiC BT power modules have been carried out. The test results confirm the simulation findings that end-of-life is mainly determined by wire-bond lift-off (Fig. 2).
Mechanical robustness analysis of inverter system
A further topic was the investigation of the mechanical robustness of the developed inverter. This was motivated by the fact that due to the direct attachment on the electric motor, high mechanical and vibrational loads are expected throughout the lifetime, in particular for the targeted construction equipment applications. For this reason, virtual prototyping was done by building up a simulation model of the complete inverter system in order to investigate its response with respect to different mechanical loadings. For calibration and verification of the simulation model, experimental modal analyses have been performed. The results show that the first three resonance frequencies of the large control PCB board are located in the maxima of the loading spectrum of the targeted construction vehicle. With this knowledge, design optimization guidelines, i.e. additional fixation points for the control PCB, could be defined in order to drastically reduce the maxima and hence, finally to improve the robustness of the overall system, as simulation results for the improved inverter model have confirmed (Fig. 3).