Active and passive thermal cycles for automotive applications
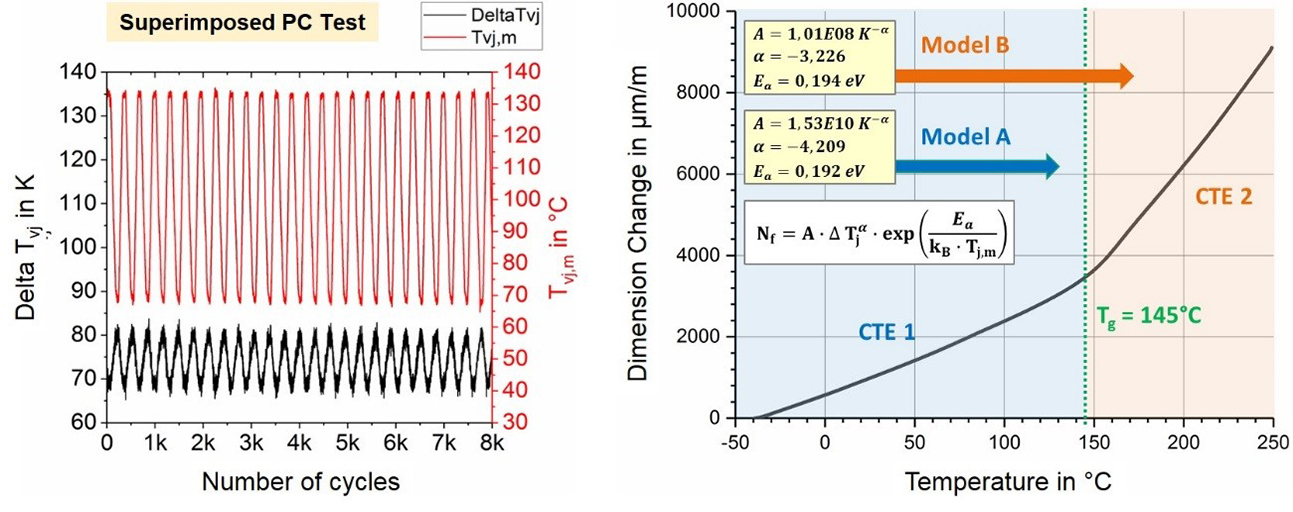
Lifetime modelling of power electronic (PE) devices and modules is an important aspect of reliability research and is typically based on power cycling tests (PCT). Thereby, the basic test principle is to actively induce power losses in the device in order to trigger realistic temperature distributions within the package. Ultimately, this will lead to the typical failures, such as die-attach degradation or failures in the chip top side connection. In the frame of an extensive study, different PCT profiles were applied in order to investigate the dependency of different load factors on the lifetime of various discrete power electronics devices, such as junction temperature swing, absolute temperature level or heating time. An adapted version of the well-known LESIT equation, which includes a Coffin-Manson related term and an Arrhenius term, was used for fitting the experimental test data. Although the derived model showed a very good agreement with the test data, it was not able to predict the test results of additionally performed PCT that were superimposed with passive thermal cycles. Those tests provide an even better representation of the actual service conditions than the standard tests. A more in-depth analysis revealed that an explanation could be found in the influence of the mold compound, more precisely in its glass transition temperature Tg. I.e., the modelling had to be divided into two groups: one including only test cases with applied test temperatures below Tg, and the other one including test cases with temperatures exceeding Tg. Using this grouping, it was finally possible to predict the lifetime of the superimposed test results much better.