Intense2020 – Development of robust acceleration sensors for automotive applications
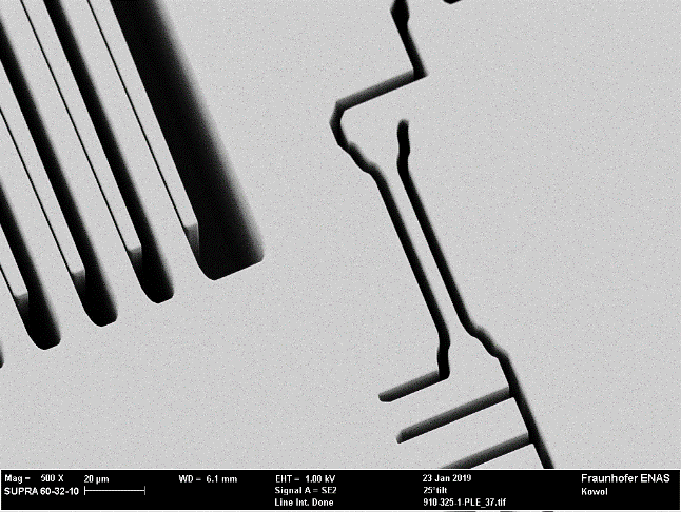
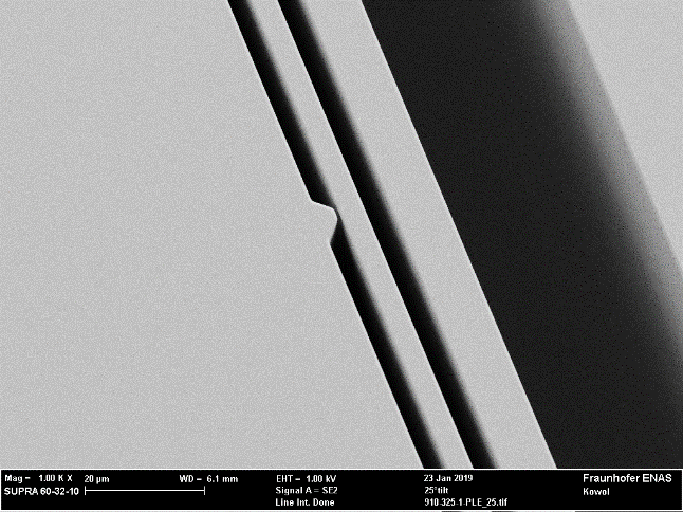
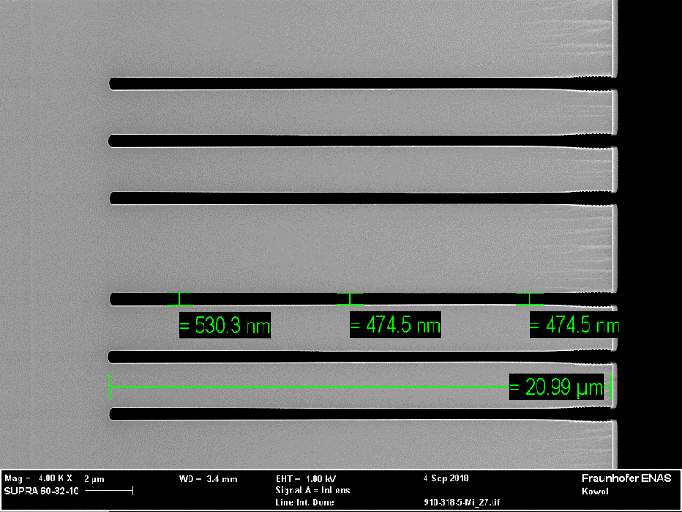
In February 2018, Fraunhofer ENAS together with the Center for Microtechnologies (ZfM) of the Chemnitz University of Technology and the industrial partner Infineon Technologies Dresden have started a research and development project on acceleration sensors. These sensors will have large measuring ranges (up to 500 g) as a well as a high shock resistance (> 3000 g in use) and aim for the application in autonomous driving systems. The acceleration sensors will be part of in-tire systems together with Infineon pressure sensors. With the required resolution these sensors will provide relevant insights on the cars speed, the road condition and even the current position of the tire. This requires the detection of accelerations in all three directions integrated in one MEMS chip.
The research partners from Chemnitz are working on innovative solutions for sensor design, such as robust design of the flexible suspension of inertial masses and flexible movement stoppers. The ongoing minimization of the width of etched gaps down to the sub-μm range together with the progress of increasing the aspect ratio up to approx. 40:1, very small, compact and sensitive capacitive sensor elements are developed. Technological scaling experiments of important geometric parameters based on established cavity SOI technology help to determine the technological limits of meaningful minimization. Another focus is put on concepts for minimizing stress influences by means of design and technology optimization.
For the development of an optimal low-stress encapsulation of the sensors at wafer level, integration concepts based on wafer bonding processes (direct and eutectic bonding, glass frit bonding) are being developed. They will be compared to a novel surface micromachined g-sensor with a monocrystalline seismic mass, developed by Infineon. In a first test run, sensors manufactured in Dresden were provided with an additional structured lid wafer applied by glass frit bonding. The glass frit layer was able to compensate for a height relief of more than 3 μm produced by the thin-film structure. Over the next two years, the focus will be on implementing and demonstrating novel approaches for the integration to minimize space requirements for bond and bond sites.
Together with the partner in Dresden, the sensors undergo extensive metrological characterizations. Fraunhofer ENAS, for example, has comprehensive experience in electrical and optical wafer level testing of sensor parameters such as capacitance, eigenfrequencies and quality factors. There is a setup used for electrical measurements of wafer level quality factors in the vacuum chamber on open and encapsulated sensors, the pressure dependence of this important sensor parameter can be determined and compared with the predicted and expected values. Another focus will be the characterization of system parameters of assemblies with MEMS from both production sites at Infineon Dresden and at ZfM in Chemnitz.
With solution approaches to design, technology and characterization of the new sensors, the Chemnitz partners want to make a significant contribution to the effective sensor development and thus for an improvement of the mobility and driving safety of our vehicles of the future.