Thermo-mechanical reliability aspects of high temperature interconnects by transient liquid phase soldering
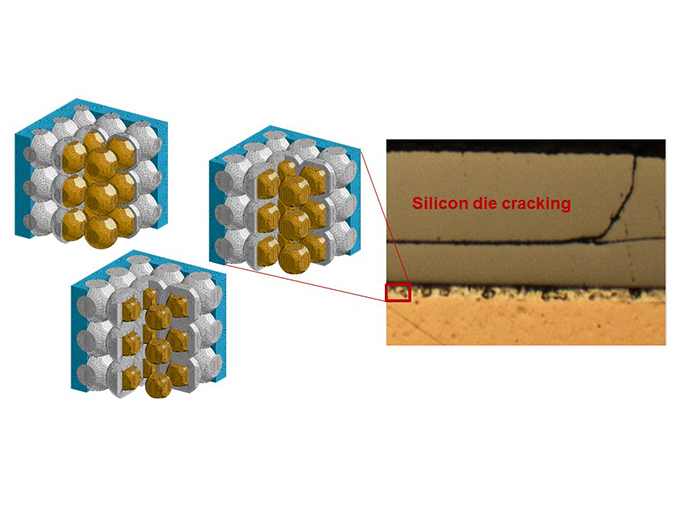
Increasing the maximum reliable operating temperature is a key issue in increased efficiency of power modules and devices applied in upcoming developments such as electrical drive systems, smart lightening, or energy management systems. In parallel to the development of semiconductors with higher operating temperatures, interconnection technologies are being developed to create solutions along the value chain. High temperature interconnection technologies in series application are silver sintering, while other sintering materials or interconnections based on the formation of intermetallic compounds (IMCs) are still under development. The latter technology can be applied in form of transient liquid phase soldering (TLP soldering), i.e. IMCs Cu6Sn5 or Cu3Sn are formed by isothermal solidification. Standard soldering temperatures (approx. 250 °C) lead to high-temperature resistant connections > 400 °C. However, material behavior of the intermetallic compounds differ from soft solders or sintered silver. In particular, they are less ductile and high mechanical stress can built up after processing or during operation. Therefore, new reliability issues due to less compliant interconnects occur and lead to silicon die fracture or metallization delamination. By use of micro-mechanical modelling tailored transient liquid phase materials can be composed to reduce the failure risk.
Project:
NanoEIS+ sponsored by VDI/VDE,
in collaboration with CWM,
FKZ: 13XP5002B