Highly integrated industrial motor drive with self-learning capabilities and EMC-compliant design
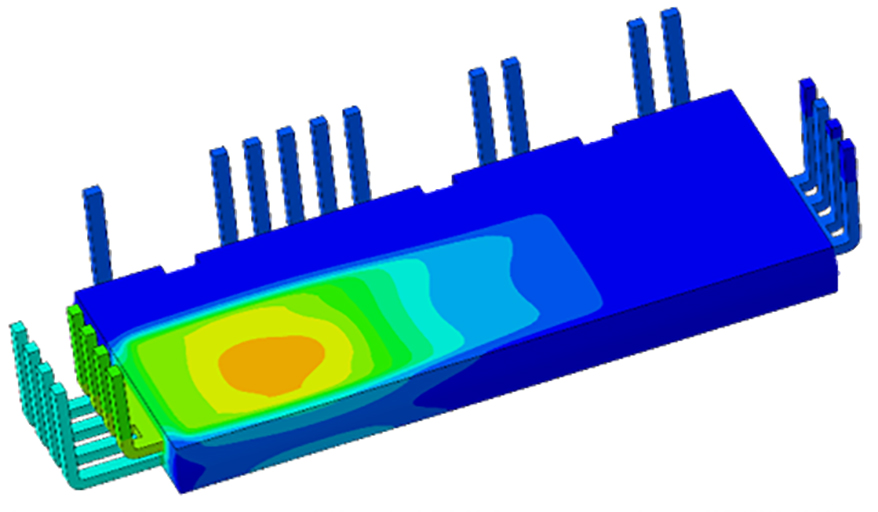
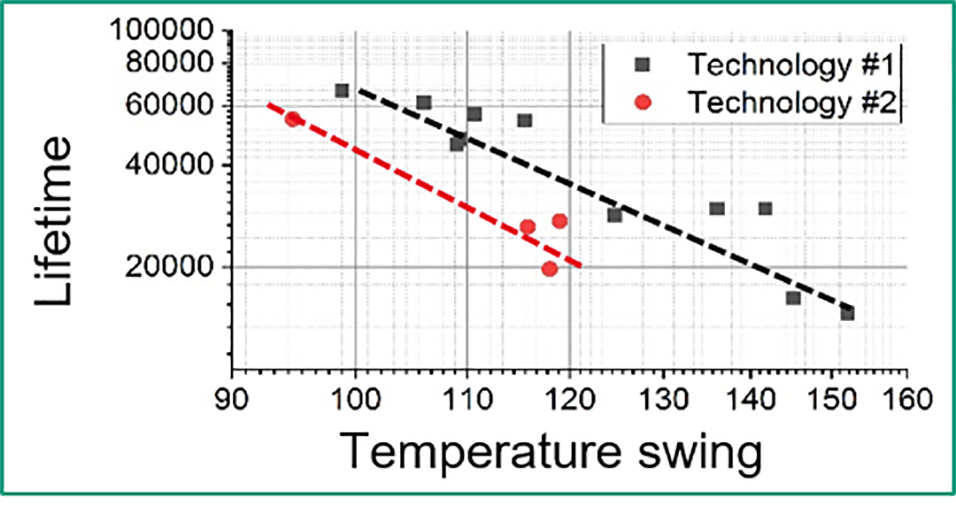
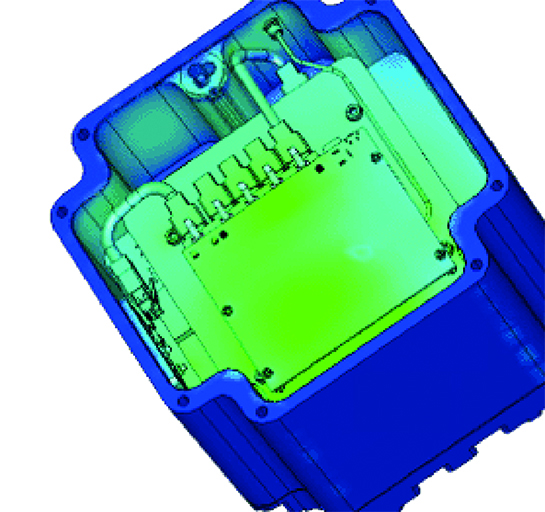
Within the recently completed PENTA project CosmoDU, a modular hardware architecture for industrial motor drives was successfully developed together with several European partners. The architecture enables full integration of the inverter and the sensors for health monitoring and drive performance optimization based on self-learning. All information are shared throughout the motor and with the higher system layers using a standard for data exchange (OPC UA), which provides a scalable and manufacturer independent way to disclose information toward the higher layers of the control and monitoring system.
Fraunhofer ENAS was responsible for assessing and improving the reliability within the motor drive integrated SiC-based power modules that were developed within the project and based on novel cooling and interconnection technologies. For this purpose, experimental investigations, incl. active power cycling tests and temperature-dependent deformation measurements, were conducted in conjunction with finite element studies in order to assess their thermo-mechanical reliability under passive and active thermal loads. The gained results are now available for the reliability evaluation of SiC-based power assemblies in future projects and cooperation.
One novelty is that all electronic components needed for the smartification of the motor are integrated into a single housing. This situation leads to a dense electromagnetic field concentration and a wide disturbing spectrum. To face occurring EMC challenges, the technique of nearfield (NF) scanning can be used. The results of a NF scan are used in two ways. First, the EMC sources can be revealed by a NF scan to fix any issue. Second, NF scanning can be combined with subsequent simulations using the NF results as a source. Merged with CAD models of further components and housings, the field radiation into other areas caused by high-frequency components can be investigated and characterized before physically integrating all components together. With this yet emerging combination of NF measurement and simulation, EMC issues can be avoided before they cause trouble after the assembly of electronic components.