
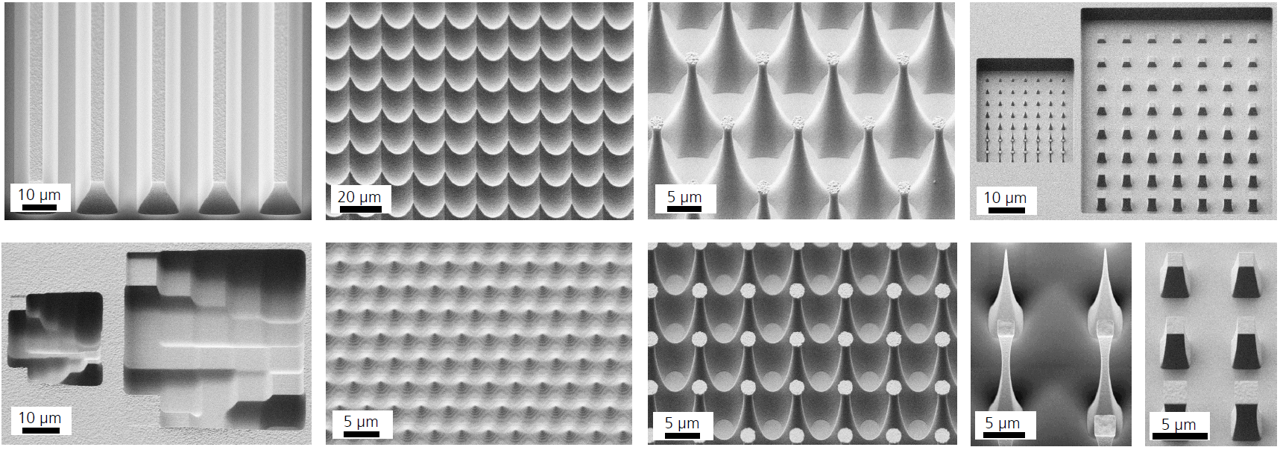
The majority of devices used today for grayscale lithography are direct laser writers, which work without a mask. The advantage here lies in the flexibility; changes can easily be made to the design. However, this process is unsuitable for the production of large quantities.
This can be remedied by i-line grayscale lithography. Even today, i-line steppers, which usually deliver a resolution of up to 350 nm, are still used in the industry for the production of microchips. Grayscale lithography is made possible by the use of so-called “pixelated sub-resolution features” on the mask. The resolution limit of the stepper is utilized here. These masks are written using an electron beam and filled with structures that lie below the resolution limit of the system (350 nm). These structures are then no longer imaged sharply, but the light intensity can now be controlled via their degree of occupancy. This makes it possible to divide the desired layout on the mask into many small sections, each of which has its own exposure intensity; these different intensities are referred to as grayscale levels. This makes it possible to utilize another “dimension” and create positive slopes. For success, it is important to use suitable resists with a low contrast, compared to the usual high contrast resists for binary lithography.
Usually the adjustment of the grayscale masks is done in several iterations to the chosen resist system and substrate. By recording contrast curves, the resist response is measured and implemented in subsequent masks. This allows flank angles to be set precisely. Through close cooperation between Fraunhofer ENAS and paint manufacturers and design companies for grayscale masks, several resist processes have already been evaluated. This allows customers to save time and therefore money when implementing grayscale in their own designs.
This technology can be used to make existing processes more flexible and save process steps. A very simple example would be the integration of different height levels in one plane and subsequent transfer by means of etching. However, new, previously unrealizable 3D geometries can also be implemented. The direct use of the paint mask without structure transfer is also conceivable.