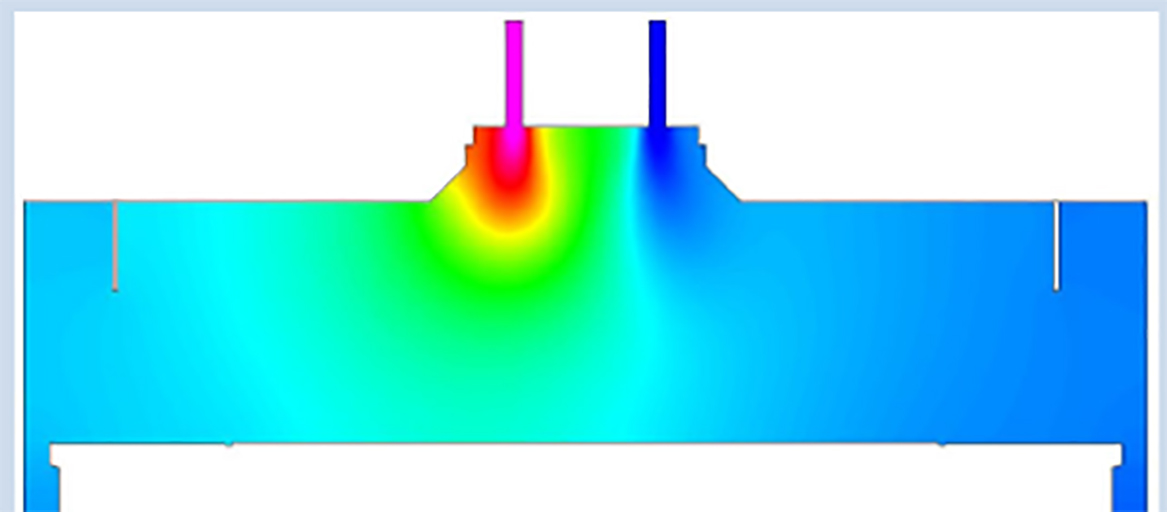

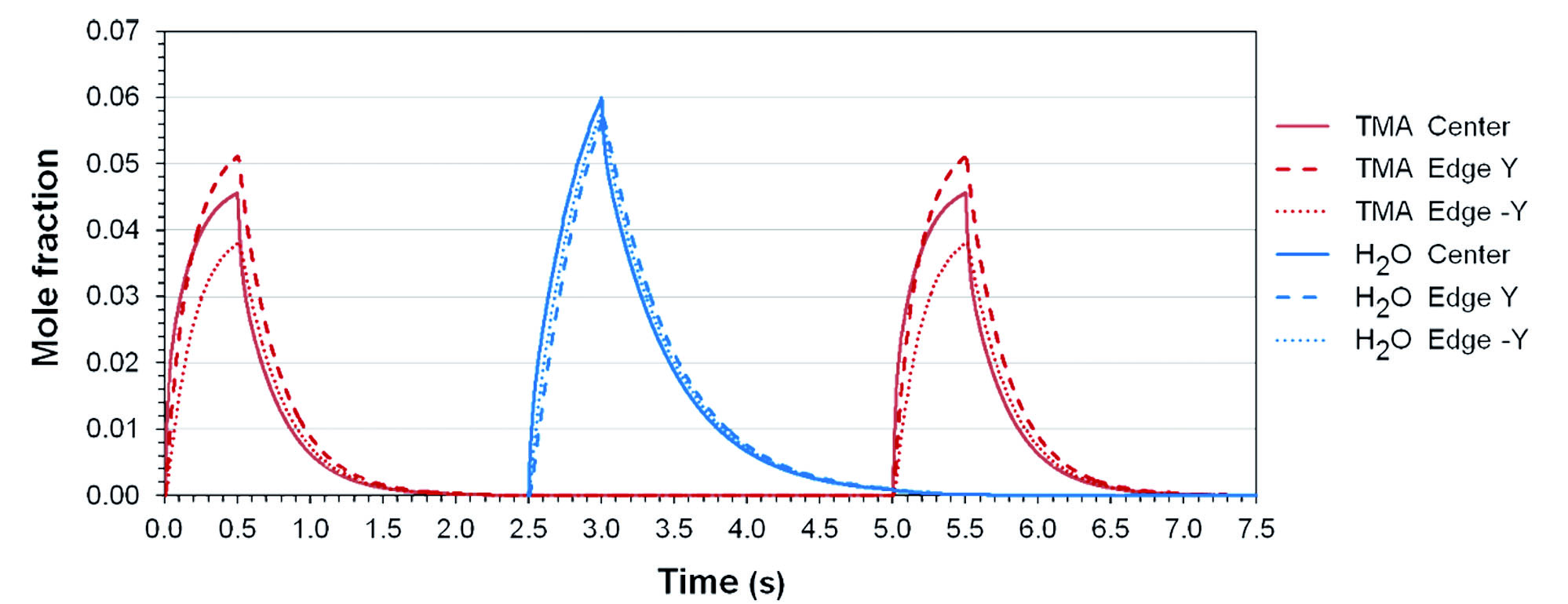
The progressive downscaling of microelectronic devices leads to an increasing demand for deposition technologies which can produce uniform, homogenous and ultrathin layers. Atomic layer deposition (ALD) has the capabilities to produce such layers even in features with high aspect ratio. The quality of the resulting layers from ALD processes depends strongly on the used process parameters. Important parameters are surface temperature, process pressure, inflow conditions, dosing, and purging times. At the Fraunhofer ENAS we use computational fluid dynamics which simulate the ALD process on the reactor scale to analyze and optimize the parameter influence.
Capabilities of reactor scale simulation
Reactor scale simulations are based on solving conservation equations for mass, momentum, energy, and species. To solve the resulting system of equations it is necessary to supply initial and boundary conditions. Furthermore, information about reactor geometry, flow physics, thermodynamic and transport properties of all fluid species and surface reactions are required. The flow physics in a reactor is complex, therefore a fine discretization in space and time is required. Since the resulting number of cells can become very large, reactor scale simulations are often computationally expensive. Therefore, parallel simulations are performed using high-performance clusters.
Results from reactor scale simulations contain information about flow field, pressure, temperature, and precursor distribution. Transient simulations reveal how the precursor gets distributed in the reactor over time. This helps us to identify regions or corners where the precursor gas gets stuck due to recirculation or to judge whether or not a shower head is configured correctly. Transient simulations also yield information about time scales. This shows us how fast a precursor is distributed and purged and allows us to define minimal process times for dosing and purging steps.
Application of reactor scale simulation - AL2O3 ALD
We investigated an Al2O3 ALD process using trimethylaluminum (TMA) and water. Experiments showed nonuniform Al2O3 deposition for this process. Therefor we used a reactor scale simulation to evaluate the purge time efficiency. In this investigation surface reactions were omitted as the reactor fluid dynamics was the key interest. A single wafer reactor was used (Fig. 1). The precursor and co-reactant inlets are arranged in an eccentric fashion at the top of the reactor. This leads to a nonuniform precursor distribution in the ALD reactor (Fig. 2). To evaluate the efficiency of the purging steps a transient analysis was conducted. The transient analysis of this ALD process showed that the chosen purging times of 2 s are sufficient (Fig. 3). As a result we concluded that the chosen purging times are not the reason for the nonuniform ALD process.
Reactor scale simulations are a useful instrument in understanding ALD reactor flow. Simulation results help us to understand the complex gas flow much better than experimental observations could. Reactor scale simulations show regions where optimization is possible and can also explain nonoptimal ALD results like nonuniform deposition or a low growth per cycle. Especially in developing new ALD processes reactor scale simulations are a key tool.